By Dan Rubinstein
It looks like a giant bowling ball, or maybe a conceptual art installation. The black fibreglass sphere, with a matte finish and a diameter of nearly three metres, commands attention in the middle of a large lab in the Mackenzie Building, at the heart of the Carleton campus.
The sphere – a work-in-progress that will soon become a state-of-the-art flight simulator, the only one of its kind in Canada – has several impressive features.
When operational, it will be able to rotate freely in any direction and simulate an airplane spin or inversion, dangerous situations that cannot be replicated by conventional pilot trainers. Because of this unlimited range of motion, the cockpit instruments and display screen are powered by battery and wirelessly linked to the control console. A novel orientation system has also been developed: a camera reads the bar codes scattered around the surface of the sphere and this data, combined with information from an internal sensor, can determine the sphere’s position and motion.
But the most remarkable thing about the Carleton University Simulator Project (CUSP) is that it has been designed and built almost entirely by engineering students — an accomplishment that showcases a commitment to combining classroom learning with hands-on engineering in collaboration with industry and government, the hallmark of an aerospace education at Carleton that was enshrined at the start of both the graduate and undergrad programs.
CUSP fits perfectly into this tradition. It began in 2002 as a team project for fourth-year students. Every engineering undergrad at Carleton gets immersed in a major design project in their final year. Options for students in the Department of Mechanical and Aerospace Engineering include space satellites, gas turbine engines and unmanned aerial vehicles.
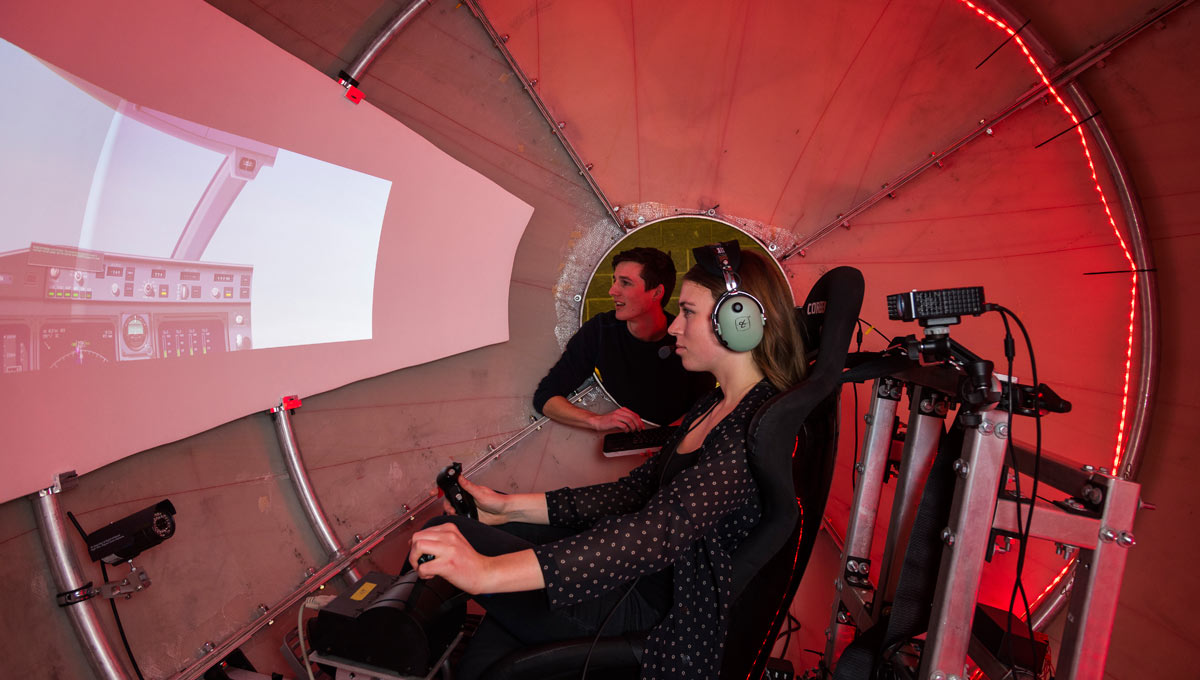
Initially, these capstone projects, which culminate in a review by external experts, were intended to last for a few months. Increasingly, however, they carry over from one group of students to the following year’s class. And that can be a very complicated process.
“It’s like a small company where you have 100 per cent staff turnover every year,” says Rob Langlois, the professor who supervises CUSP, the longest running capstone project on campus. “But it also offers many rewards.”
Students learn the value of teamwork, project management and detailed documentation. They get a feel for the long-range timelines that define the aerospace sector. And they interact with professionals from public agencies such as the Canadian Armed Forces and companies like Montreal-based global simulator leader CAE and TRU Simulation + Training, connections that can help kick-start careers.
Roughly 325 undergrads, 15 faculty members and a handful of grad students have worked on CUSP since its launch.
“As the project gets more complex, the learning curve gets steeper,” says Langlois. “All of the fourth-year projects are attractive to students, but CUSP is especially attractive because it’s so challenging.”
This sentiment embodies Carleton’s aerospace program, which draws the best and brightest students and faculty from across Canada and beyond precisely because of the challenges it provides. And the payoff that has held true since the start of the program — an opportunity to play a role in an important national industry and a growing regional aerospace cluster — is a big part of the appeal.
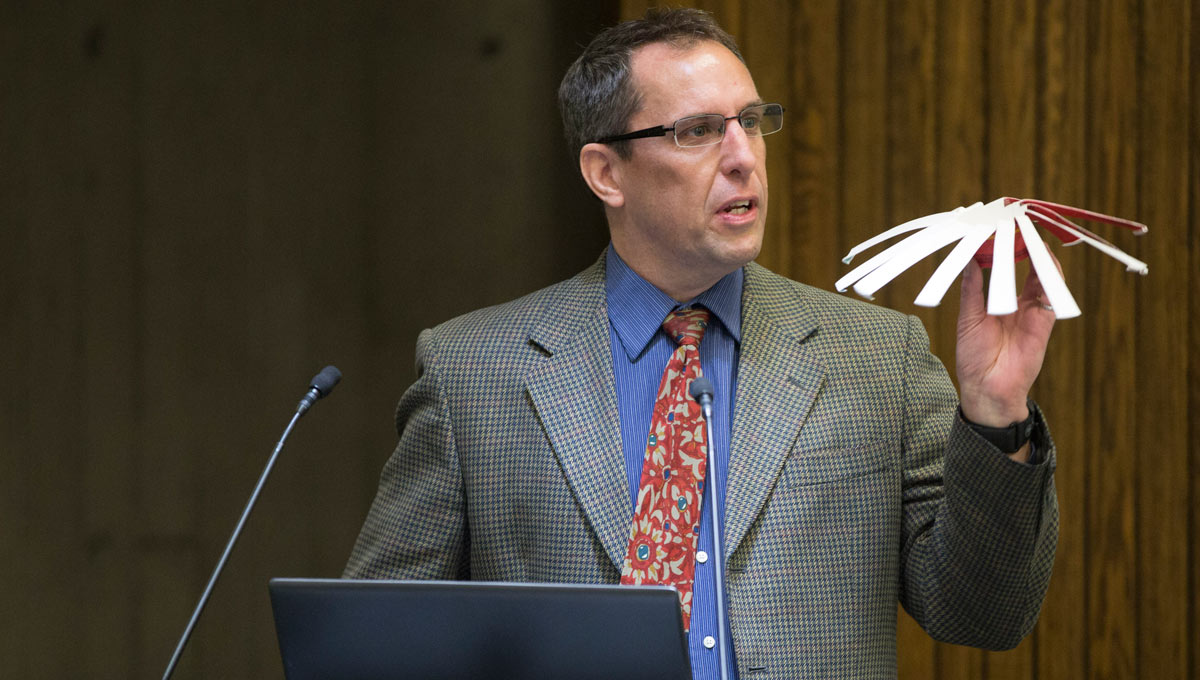
Carleton professor Robert Langlois
Carleton has one of the largest and most comprehensive aerospace research programs in the country, with unique facilities and faculty who work both on campus and with external partners. Students tackle major projects and are often supported by scholarships; they spend a lot of time in labs and on co-op placements with government and private sector employers.
In this industry, innovation is the key to international competitiveness. Thanks to their technological edge, Canadian organizations already punch above their weight around the world. To continue — and enhance — this success, the next generation of students and researchers must be ready to embrace the challenge.
In 1945, three years after the birth of Carleton College, a two-year certificate program in engineering was established. The institution’s approach to the discipline evolved as the college became a university and moved to its current campus beside the Rideau Canal, a UNESCO World Heritage Site.
Carleton’s School of Engineering was created in 1957, with a four-year program replacing a two-year certificate. In 1961, when the first engineering degrees were granted, a graduate program in aeronautical engineering was launched, although students could already take aeronautical undergraduate courses.
Three years later, the first two blocks of the Mackenzie Building opened. With narrow bunker-like windows, it was nicknamed “Fort Ruptash,” a nod to Carleton’s first engineering dean, John Ruptash, who had earned his PhD from the Institute of Aerophysics at the University of Toronto — a hint of the growing role of aerospace within the university’s engineering portfolio.
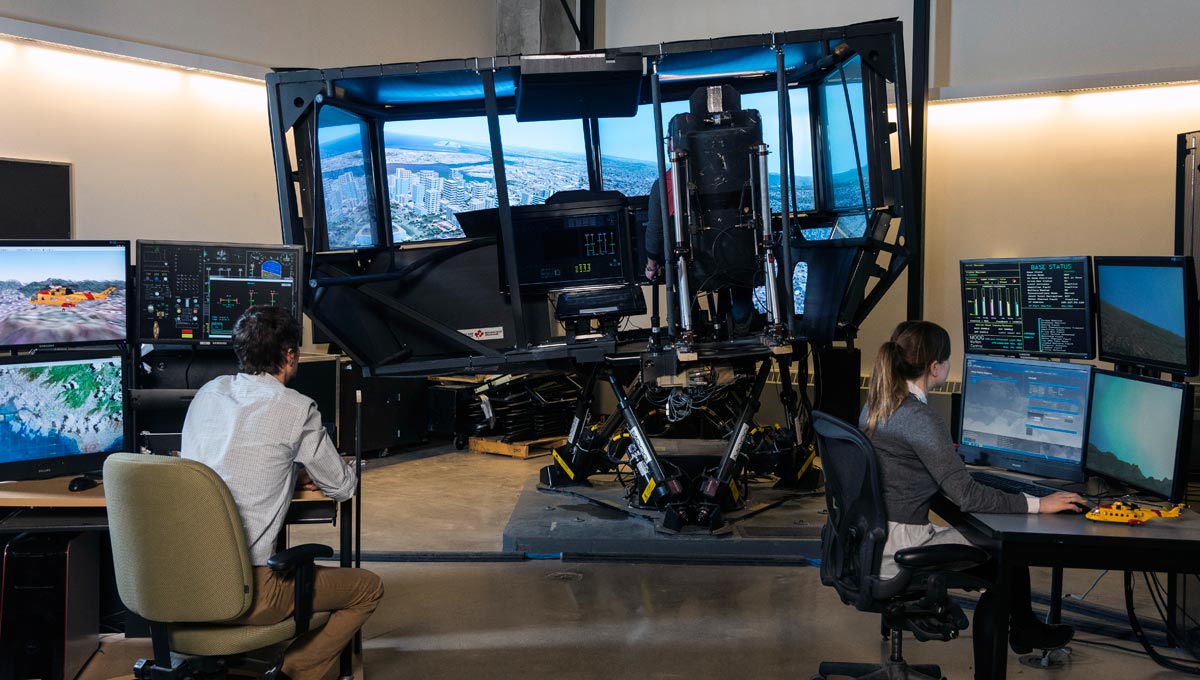
There have been many leaps forward since then, including the creation of the Department of Mechanical and Aeronautical Engineering in 1970, but the biggest change was sparked in the spring of 1986.
The engineering faculty held a retreat at the historic Opinicon Resort on the Rideau Canal an hour and a half southwest of Ottawa. At this blue-sky gathering convened by then engineering dean Spruce Riordon, the group discussed how their faculty could expand and grow.
“We should start an aeronautical program at the undergraduate level,” suggested professor Bill Rainbird, who had chaired the Department of Mechanical and Aeronautical Engineering in the past.
“Yes!” responded professor Dick Kind, the chair-elect at the time, a researcher and teacher who played a central role in the development of the program. “What a good idea.”
Aerospace was a burgeoning niche in Canada’s tech community. Ottawa — home to the National Research Council (NRC), Transport Canada and other government enterprises — was well-situated geographically, close to the industrial hubs in Montreal and Toronto.
Prof. Steen Sjolander, who is still a key member of the aerospace faculty, wrote the formal proposal that Carleton’s Senate would eventually accept. In 1988, the university established Canada’s first Bachelor of Engineering program in aerospace engineering.
Part of Sjolander’s proposal was a name change from “aeronautical” to “aerospace” — a recognition that although space accounted for roughly 10 percent of the industry in Canada, it had symbolic power. It represented a new frontier.
In 1990, Doug Staley, who had managed the team that created the control system for the space shuttle’s Canadarm while working at Spar Aerospace, was recruited to create and teach a spacecraft design course and lead the space stream. An independent consultant at the time, he received a cold call from Kind asking if he wanted to join the faculty — a fruitful practice, recruiting industry experts, that has continued at Carleton over the years.
At the time, Canada’s aerospace industry had an annual budget of about $5 billion and employed some 45,000 people. It was the fifth largest in the “free world,” according to a Carleton engineering publication, after the United States, United Kingdom, France and West Germany.
Beyond aircraft projects and communications satellites, aerospace engineers worked in government research labs and for the military, and in a range of related fields, including the design of tall buildings and large bridges (where wind loads and aero-elastic behaviour are important considerations), and in the automotive and rail industries (where the need to reduce weight and drag led to the use of aircraft structural design techniques, materials and testing methods).
The fledgling program’s initial target enrollment was 30 students, although 15 would have been decent. They got 45 students from across Canada.
Today, Carleton Aerospace boasts the largest cohort of undergrad aerospace students in Canada, 125 per year, and the largest population of grad students, 80, under the tutelage of the largest group of aerospace professors, 30.
“Students came beating down the door, and they were absolutely top notch,” recalls Kind. “We got outstanding people and we worked them hard. It was clear, right from the start, that the program was a major success. It became a flagship program for Carleton, and it still is. I may be biased, but I think we got it right.”
See “Origins of Carleton Aerospace”
One of the things Carleton Aerospace certainly got right from the start was bringing in promising researchers to build the program. One of the early arrivals was Herb Saravanamuttoo.
Born in Glasgow, Scotland, Saravanamuttoo came to Canada in 1955 to work for Orenda Engines on the Avro Arrow project — a made-in-Canada fighter jet with the promise of reaching a speed of Mach 2 at an altitude of 50,000 feet. The legendary plane was supposed to serve the Royal Canadian Air Force for decades to come.
Saravanamuttoo, a gas turbine engine specialist, was working on the Iroquois engine in an Orenda computer lab on Feb. 20, 1959, a date seared into his memory. The plant’s public address system didn’t broadcast in the lab, so after hearing a muffled announcement from a loudspeaker in the corridor, he stepped out of the lab to ask a colleague what was happening.
“You’re fired,” the man replied.
Saravanamuttoo was among the 14,000 people let go when the Avro Arrow program was killed — a day that has gone down in Canadian aerospace infamy.
Unlike the plane, whose plans were destroyed along with all existing airframes and engines, Saravanamuttoo rebounded quickly. He spent a couple years with Orenda’s nuclear group before starting on industrial gas turbines, then went back to the U.K. and earned his PhD at the University of Bristol while working with Rolls-Royce on the engine for the Concorde supersonic passenger jet, using knowledge and expertise from his Avro experience.
Saravanamuttoo was happily settled down with no intention of returning to Canada, but his wife had a friend at Carleton, and Saravanamuttoo flippantly asked the friend: “Any jobs there?” Two days later, he got a call from Don George, who had succeeded John Ruptash as dean of Engineering. In 1970, he joined Carleton’s engineering faculty.
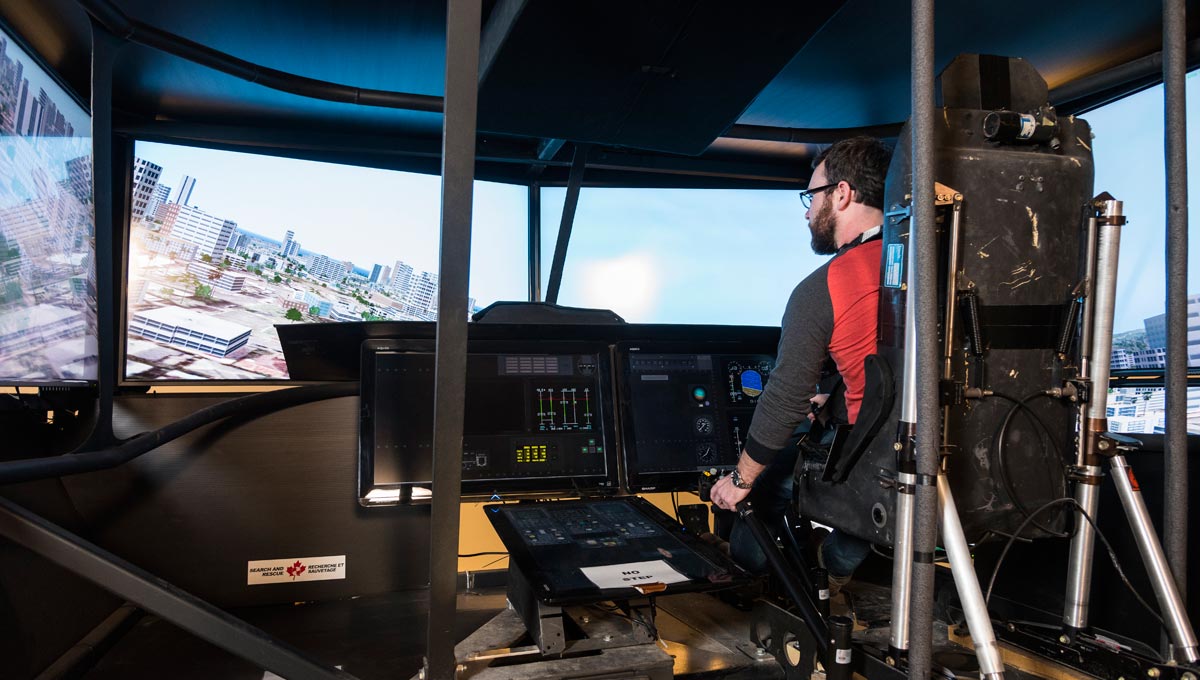
Throughout his tenure in academia, Saravanamuttoo has always maintained close ties to the aerospace industry. He has served as a director and longtime associate of Ottawa-based critical machinery company GasTOPS, founded by his former grad student Bernie MacIsaac and currently run by another of his former students, David Muir, two of the many Carleton grads who have worked at GasTOPS over the years.
Saravanamuttoo has conducted research at the NRC with his grad students — “back then, the NRC had equipment but not a lot of bodies; we had a lot of bodies but not much equipment” — and developed and delivered a short course on gas turbine engines for a who’s who of multinational clients, including Rolls-Royce, Airbus, Pratt & Whitney Canada, Siemens, Caterpillar and Honeywell.
These courses, delivered around the world, have helped enhance Carleton’s global reputation. They “extend the work of the departments and faculty,” then vice-president (Academic) James Downey wrote in a 1979 memo, “into their academic, scientific and professional communities.”
Along with fellow Carleton Prof. Paul Straznicky, Saravanamuttoo is also a co-author of the definitive textbook on gas turbine engines: Gas Turbine Theory, originally published in 1951, is now in its sixth edition, with a seventh on the way. “The gas turbine is unquestionably one of the most important inventions of the 20th century,” declares the introduction, “and it has changed our lives in many ways.”
“I keep telling my students that stuff like fluid dynamics and thermodynamics stays the same forever,” says Saravanamuttoo. “The basics always stay the same.”
During a sabbatical away from his post at Carleton, where he chaired the aerospace program for 10 years, Saravanamuttoo worked with the British Royal Navy on engines for ships that sailed in the Falklands War. One of his students took Gas Turbine Theory to sea on HMS Sheffield, which sank in battle. “So there’s a copy of my book at the bottom of the Atlantic,” says Saravanamuttoo.
Despite officially retiring in 1998, he remains a professor emeritus and continues to teach at Carleton. “The basic game plan is that I keep lecturing until I drop dead. I do it because I like it — I came to the university because I wanted to teach.”
And because he understands the importance of passing on knowledge, a lesson learned the hard way when the Avro Arrow was grounded forever.
The start of Carleton’s undergraduate aerospace program was buoyed by the arrival of Straznicky, who joined the faculty in September 1989 and has served as another bridge between the university and industry.
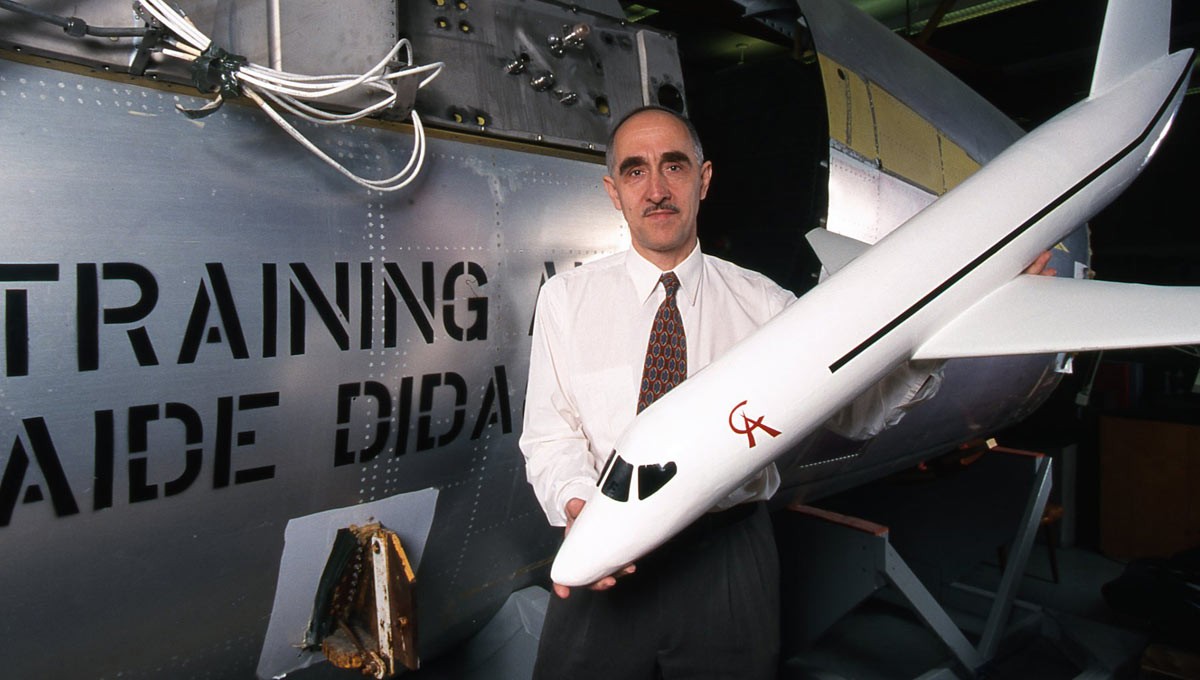
Carleton professor Paul Straznicky
He had been working for a Toronto-based wind tunnel design company on projects in places like NASA’s Ames Research Center in California and Porsche’s R&D centre in Germany. But there was one thing conspicuously absent from his impressive resume — he did not have a PhD.
Born in Czechoslovakia and smitten by Sputnik, Straznicky followed his obsession with rockets into engineering. After emigrating to Canada in 1970 and working as a carpenter, he found employment in his field and developed an expertise in aerospace materials.
Straznicky enjoyed his job in Toronto and rose through to ranks to become vice-president at now-defunct DSMA International, where Steen Sjolander worked and later served as an aerodynamics consultant. When the aerospace bachelor’s program at Carleton was born, Sjolander recruited Straznicky because of his professional experience. The university needed somebody to manage the fourth-year projects.
“I thought it was a joke,” Straznicky says about the initial offer from Carleton. “I didn’t take it seriously because I don’t have a doctorate.”
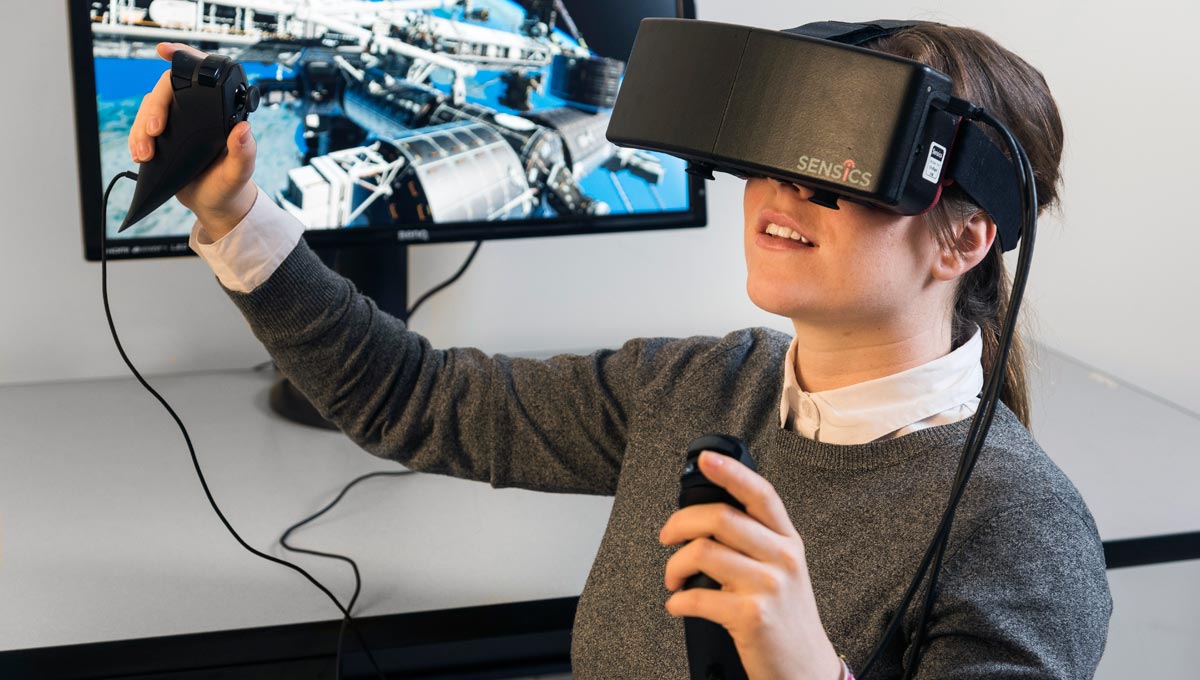
But Sjolander was persistent, and after visiting Ottawa, Straznicky made the jump. Quite quickly, at the reins of the capstone projects — which employ a team approach that is unique to Carleton, a pioneering approach to experiential learning — he hit his stride.
“People in industry know how to work as part of a team,” says Straznicky. “Very rarely does one sit in a cubbyhole doing work on their own. These projects are a very realistic simulation of a real-world working environment. They give students a taste of what is to come.”
The first major design project he helmed was an unmanned aerial vehicle (UAV) for Quebec’s forest fire service. Over the years, other small aircraft, such as business jets and helicopters, were also designed.
Initially, the projects were purely conceptual, but as they evolved, they became more tangible. A subsequent UAV project in the early 2000s, for example, led to the construction of a fully functional UAV in partnership with Ottawa-based Sander Geophysics, an airborne geophysical survey firm with a fleet of airplanes.
Sander provided some funding and supported graduate students who were brought in to help undergrads. The project, like CUSP, continued beyond one year.
CUSP and the UAV project tap into two of Carleton’s aerospace research strengths. The program, which is divided into four streams (aerodynamics, structures, avionics, space systems), has eight official areas of expertise.
See “Areas of Research Focus”
Just like Saravanamuttoo, Straznicky is officially retired but continues to teach. Like Saravanamuttoo, his students have always had exposure to industry and government research labs and gone on to solid careers. (Jeremy Laliberté, the current director of Carleton Aerospace, was one of Straznicky’s PhD students.)
After the Aloha Airlines accident over Hawaii in 1988, for instance, where part of the fuselage peeled off in flight, Straznicky and his students joined an investigation at the NRC, with their work helping to address the issue of metal fatigue in aging aircraft. “As they age, they’re like us,” he says about airplanes, “they start to crack up.”
All of this is a testament to the hands-on experience Straznicky and so many of his colleagues have brought to the program. “This is why what they try to do now is get somebody with a PhD and industry experience,” he says, “to get the best of both worlds.”
To understand how aerospace research and education at Carleton fit into the wider world, it’s helpful to take a trip across Ottawa to the NRC headquarters in the east end of the city.
In building M13 — one of more than four dozen buildings on the sprawling campus off Montreal Road — Carleton alumnus and adjunct professor, Rick Kearsey, works as the leader of the NRC’s Materials and Component Technologies group.
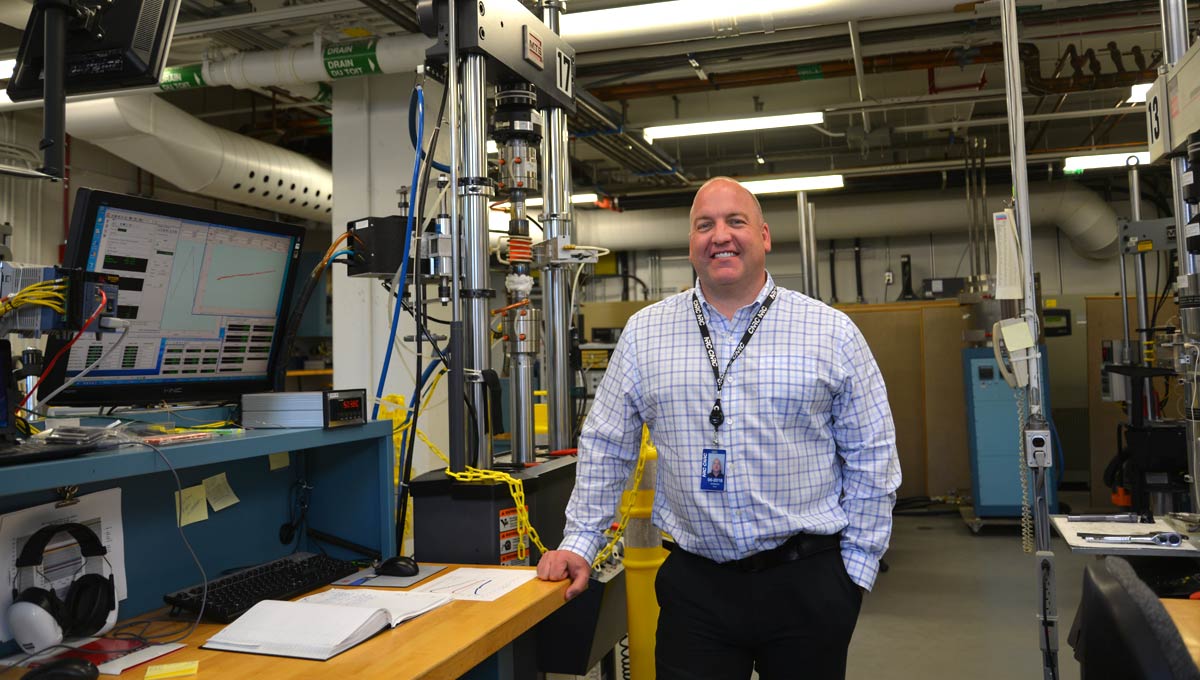
Carleton alumnus and adjunct professor Rick Kearsey
The low-rise building, a collection of offices and labs, is dedicated to the study and development of high-temperature engine materials. Kearsey, an affable Newfoundlander who earned both his PhD and master’s in aerospace engineering at Carleton, is focused these days on designing non-metal ceramic matrix composites (CMCs) that can withstand temperatures as high as 1700 C.
In the basement of M13, Kearsey points out induction heating coils and furnaces used to test how CMCs respond to such extreme heat. These strong but lightweight materials represent the future of gas turbine engine design.
To maximize fuel efficiency, these engines burn at extremely high temperatures. Their components — and there are roughly 40,000 parts in a 747 engine, for example — must be able to handle the heat in the hot section of the engine.
Making parts that are durable and will last for a long time, with minimal maintenance, will save the airline industry millions of dollars. But safety is the ultimate consideration, says Kearsey. “If an engine fails, a plane can fall from the sky. There is no room for error.”
The R&D work that Kearsey is managing through his team at the NRC, with the support of a pair of Carleton graduate students, will take years of effort and cost millions of dollars. But the materials developed could end up not only in airplanes, but also car engines and nuclear reactors. And none of this would be possible without the NRC’s university partners.
“Almost everything that’s of value that we do at the NRC came from grad student research,” says Kearsey. “When you work with a PhD or master’s student, you spend as much time as you can on a three-year or five-year project. The real hardcore fundamental research is almost always done in tandem with a university.”
Proximity to Carleton brings a flow of summer, grad and co-op students to the NRC. Carleton students, says Kearsey, hit the ground running.
“The key is that Carleton profs are heavily involved with industry, so they bring real-world problems to the classroom.”
“Our relationship with the national aerospace research labs that are here in Ottawa, it’s not just geography,” affirms Laliberté, who was a visiting researcher at the NRC after finishing his PhD at Carleton and now supervises several grad students who are visiting workers at the NRC.
“We’ve got the talent and the students. It’s a close connection with a lot of history, much of it based on the university being able to send people there. It’s not so much about money and funding — it’s a partnership between people: grad students, co-op students, research scientists and faculty.”
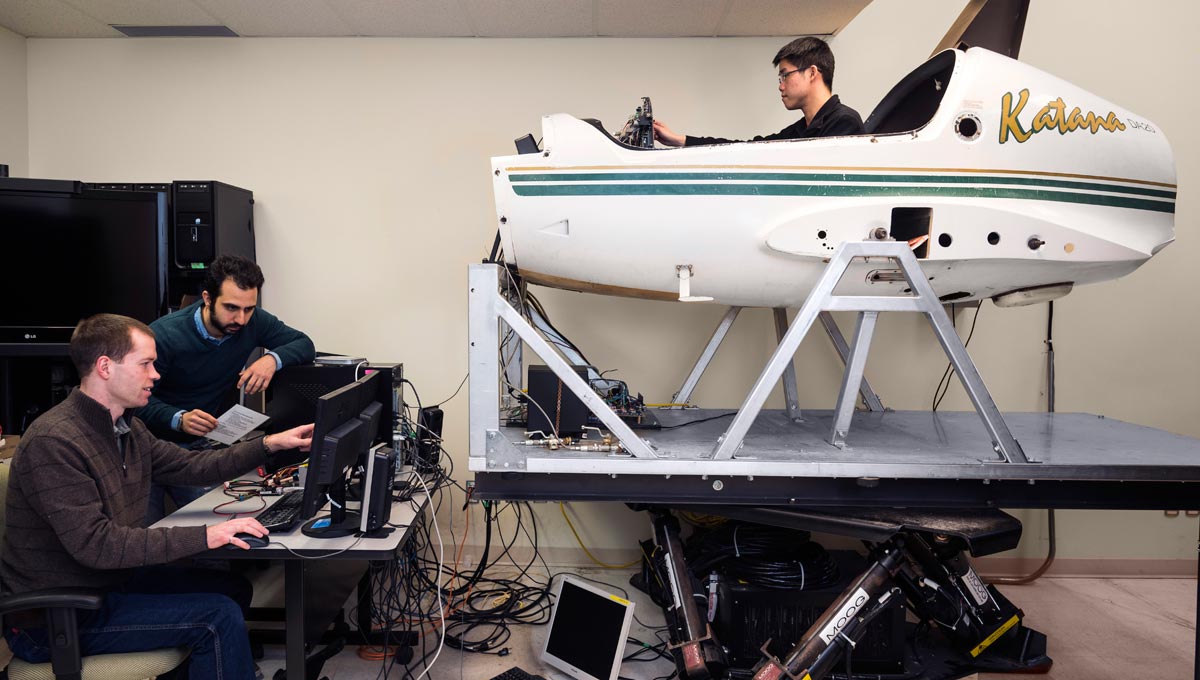
The NRC is not the only national institution with close ties to Carleton, of course. The university and NAV CANADA, for example, recently signed an agreement to work toward establishing an Aerospace Centre of Excellence in Cornwall, Ont.
Potential programs to be offered in the existing NAV Centre campus in the city on the St. Lawrence River will include professional certification courses in the areas of drones, pilot training, air traffic management and airport management. It is expected that additional programs will be offered in the near future.
“One of Carleton’s central goals is to work with neighbouring communities,” Carleton President Roseann O’Reilly Runte said when the agreement was announced last fall. “This entrepreneurial initiative brings together the knowledge and skills of those working at NAV CANADA and Carleton University in support of economic development. Together we will foster regional and international growth through education.”
“We want to provide leading-edge programs that anticipate the next era of aviation,” added Rafik Goubran, dean of the Faculty of Engineering and Design. “This will improve Canada’s position in the global aviation market.”
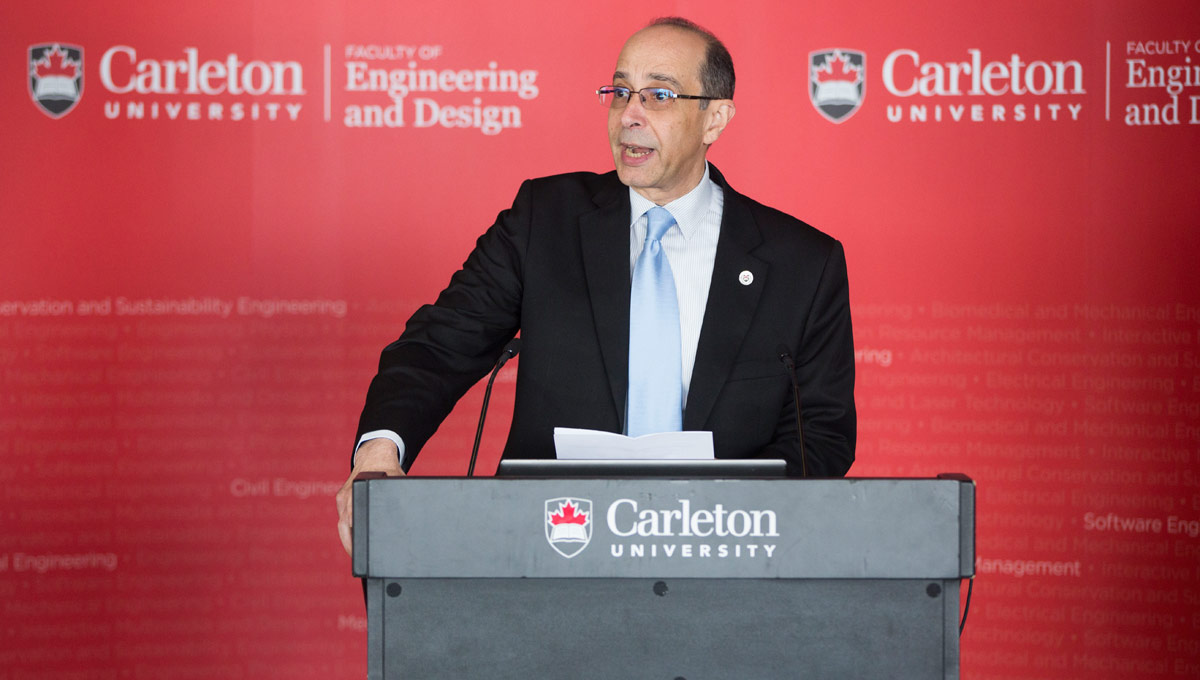
Rafik Goubran, dean of Carleton’s Faculty of Engineering and Design
In 2014, Canada’s aerospace industry generated $27.7 billion in revenues and employed more than 75,000 people. Indirectly, the sector contributed more than $29 billion to the GDP and employed 180,000. Three large companies come to mind — Bombardier, Bell Helicopter and Pratt & Whitney Canada — but hundreds of smaller firms are part of the mix.
Aerospace manufacturing and maintenance, repair and overhaul are some of the country’s strengths internationally, alongside dedicated research and development. Canada also leads every other Organization of Economic Cooperation and Development nation in civil flight simulation, and is third in both civil aircraft production and civil engine production.
Nearly 60 percent of the country’s aerospace exports are supply chain related. The United States is the key export market, although exports to Asia are soaring.
“In order to integrate into global supply chains, Canadian aerospace manufacturers are accepting greater risk, incurring greater up-front costs and reducing lead-time,” according to Industry Canada’s 2015 report on the state of the aerospace sector. Increased production and more innovation are crucial if these risks and costs are to pay off.
The research of Aerospace Prof. Xiao Huang addresses both of these fronts. When she talks about her work, the phrase “the future of the aerospace industry” comes up often.
Huang, who has been at Carleton since 2002, has a background in the private sector. She worked for Bristol Aerospace Ltd. and JDS Uniphase for a decade before moving to academia. At both companies, she was a specialist in materials and processes, joining and coatings. Her training in production and supply-chain management also helped JDS refine its just-in-time process for making fibre optic cables.
“It’s the type of process that’s very important these days in the aerospace industry in order to remain competitive in an international market,” says Huang, who earned undergraduate and master’s degrees in engineering in her native Shanghai before moving to Canada for a PhD in physical metallurgy at the University of Manitoba.
At Carleton, Huang is conducting research into thermal barrier coatings for gas turbine engine parts — to help ensure parts aren’t damaged by engines that run at higher and higher temperatures. Next-generation parts will involve more ceramics, she believes, reinforced by fibres or whiskers. The development and testing of these ceramic matrix composites is part of a collaborative effort between Huang and Rick Kearsey at the NRC.
Huang is also working with France’s University of Toulouse on developing better anti-icing coatings for airplanes. (Aerospace research collaborations and/or student exchanges with universities in Brazil, China, India, Italy, Turkey and other countries are under way as well.)
American airports use 40 million gallons of saltwater to de-ice planes every year, says Huang. That wastes water and generates pollution. Wings and other parts with anti-icing coating will be more resistant to ice formation, and in turn need less time on the tarmac for de-icing. One of the coatings being developed is a thermal sprayed Teflon-based coating. This technology can find its way to automakers or wind turbine manufacturers, whose surfaces can be made less adherent to ice.
“In aerospace, we develop the most advanced materials and processes and there’s a trickle-down effect to the energy, nuclear and auto industries,” says Huang. “Other fields are always on the lookout to see what’s coming next in aerospace.
“Aerospace has to have the best materials, the best performance, in addition to the best design. When something is developed, even medical fields can use it.”
There’s something else that drives Huang, however, perhaps more than the potential impact of her research. On the shelf in her office are about three dozen theses written by PhD and master’s students she has supervised.
“I could look at their names,” she says, “and tell you where they all got jobs.”
When Yosha Mendis was growing up in Sri Lanka, her father, an air force engineer, would often bring her to work. The four-year-old would stare at the runways outside his office window, fascinated by flight.
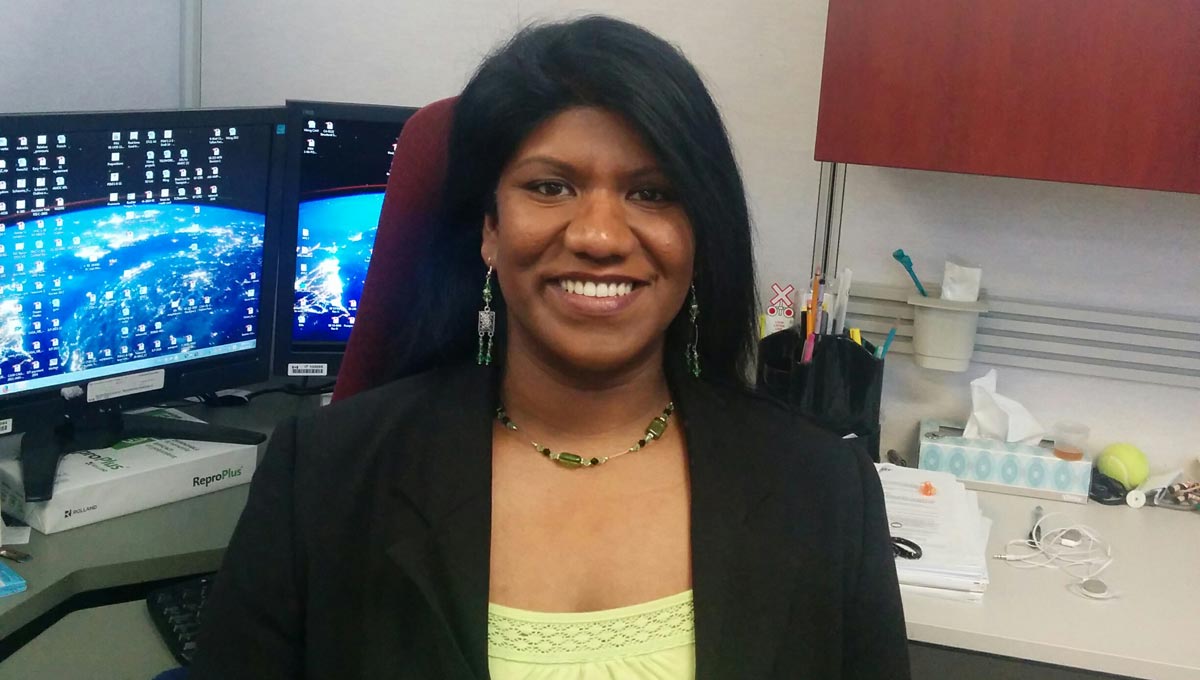
Carleton alumnus Yosha Mendis
Then her father moved to a job with Air Lanka, the national airline, and the family began to travel frequently to places such as Thailand and Singapore. Mendis was hooked. In Grade 9, after moving to Ottawa with her family, she set her sights on becoming an aerospace engineer.
“I don’t know what I would have done if engineering didn’t work out,” says Mendis, who now works on “continuing airworthiness” with small aircraft manufacturers for Transport Canada. “I had no backup plan.”
Mendis surely benefited from the extra math and science lessons her father taught every summer, but she also took woodworking and auto mechanics in high school — experience that has served her well. After an undergraduate degree at Ryerson, she enrolled at Carleton for her master’s in 2000.
“I really liked the fact that I could do experiments as part of my studies,” she says. “I didn’t want to do only computational analysis — I wanted to do straight-up experiments, not just sit at a computer.”
See “Aerospace Students Soar”
Mendis did her thesis research on the structural properties of aluminum and fibre metal laminate cylinders at the NRC; Bombardier was a partner in the project. After graduation, she found work with a series of private companies, including Spar Aerospace, before joining Transport Canada in 2009.
In her current role, Mendis works with companies such as British Columbia’s Viking Air. If there are problems with a particular plane, Transport Canada gets involved and tries to help devise a solution, as well as inspection and repair programs. The agency certifies new lines of aircraft before they’re allowed to fly, but when they’re in service, Mendis says, “they become my business.”
Even though she deals regularly with structural issues, which is her expertise as an engineer, she looks into everything from fuel systems to batteries. “You get exposed to practically everything,” she says, crediting her time at Carleton for preparing her. “As much as you specialize in one thing at school, you also get a broad education in everything.”
When he was a student at Carleton, getting into the lab was a regular activity for Metin Yaras, who chairs the university’s Department of Mechanical and Aerospace Engineering. While working on his master’s, with Steen Sjolander as his supervisor, Yaras realized that he was strong theoretically but not on the practical “nuts and bolts” side of engineering.
“Steen was a young prof and I asked him if we could go beyond theory and into the lab,” recalls Yaras. “He was kind enough to give me a chance, and I learned things from the ground up.”
Together, with Pratt & Whitney signing on as an industry partner, they built a lab where researchers could work on developing turbines that are more efficient aerodynamically. First, they had to get a better grasp of the physics, and then they came up with mathematical models that Pratt & Whitney was able to use.
After completing his master’s degree, which Yaras considered a “fact-finding mission” on where to go and what to do next, he saw that he could keep growing as an engineer — and give back — at Carleton.
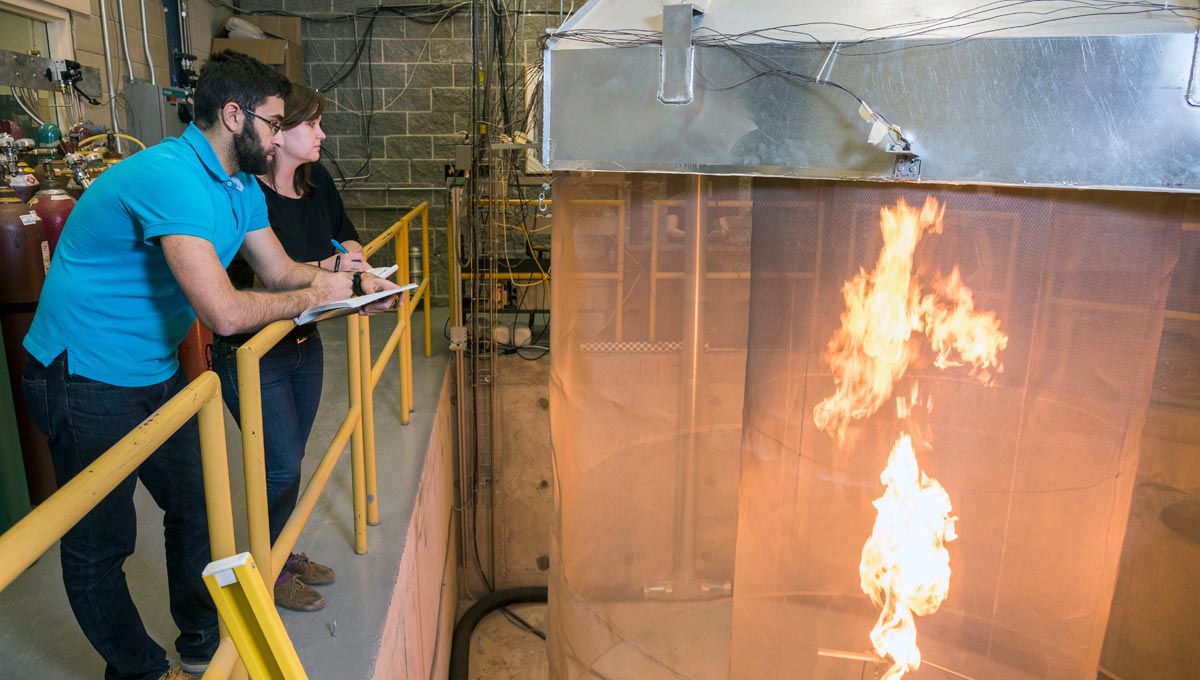
He continued to work with Pratt & Whitney while earning his PhD and after becoming a professor in 1991. Yaras developed a specialty in turbine blade fundamentals — exploring questions such as how air flow becomes turbulent and how to control it — and gained a deeper understanding of the diverse applications of this work, in fields ranging from gas-turbine engine design to wind turbines and the cooling of nuclear reactor cores.
“Whether it’s a blade in an airplane engine or a wind turbine, fundamentally you’re looking at the same questions,” says Yaras. How close together can they be arranged so they’re efficient but the wake of one blade doesn’t impact another? Can you change blade design so they’re more efficient in compact formation?
“Once you realize the cross-pollination of opportunity, you are ready to reach out to colleagues in other departments, including public policy, biology, psychology and others,” continues Yaras, who considers increasing the “critical mass” of this research unit one of his goals.
“Our department is versatile. Many of my colleagues and I can shift from one application to another.”
See “Interdisciplinary Excellence”
This versatility will be on display in the new $1.3-million Wind Induced Dynamics Lab (WInDLab), now under construction in Carleton’s Visualization and Simulation Building. The facility is being integrated into the lab space where Yaras has been conducting heat transfer research with Atomic Energy of Canada Ltd. on the cooling of next-generation nuclear reactors, and will benefit from some of the existing infrastructure, such as availability of 500 kilowatts of electricity and large-scale air conditioning units in the lab, and a cooling tower to dissipate the generated heat into the atmosphere.
The WInDLab will be a unique facility with a large-scale motion platform enabling controlled motion of models during aerodynamic testing, and will be capable of testing things such as how wind turbines perform on floating offshore platforms, how helicopters can land safely on ships at sea, and the aerodynamics of aircraft during maneuvers.
One of the purposes of WInDLab, whose project leader is Langlois, will be to conduct research on the long-term viability of wind turbines, particularly in harsh environments. It’s the kind of lab where Carleton faculty and students will be able to collaborate with their partners from industry and government to help address Canada’s long-term sustainable energy needs.
“We have to be innovative in Canada,” says Yaras. “Manufacturing has migrated to places such as China and Mexico. So, what’s our role and expertise globally? A production-line approach to making cars worked in the past, but it won’t be an economic engine in the future. What’s the next-gen car — or plane, or wind turbine — going to look like?”
Carleton Aerospace addresses these questions by hiring educators with a strong interest in research “because students get most excited when they see a leading-edge researcher in front of the class,” says Yaras, and they develop a sense of ownership.
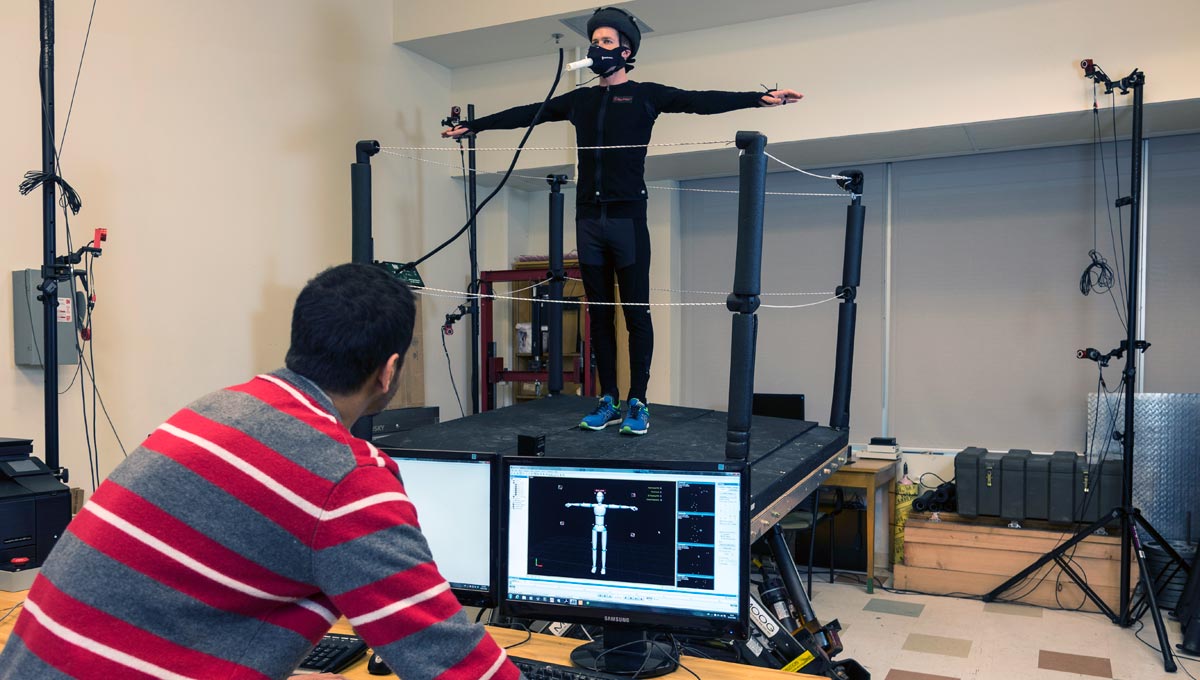
These students, such as the group working on CUSP, are the future. They belong to the generation that will pick up the ball — or, in the case of CUSP, the sphere — and run.
“I’m keen to see more long-term vision in the aerospace sector, and not just look at immediate needs, because it’s a very significant part of our economic landscape,” says Yaras. “If we don’t advance these technologies, somebody else will.
“We have a footprint globally, but what can we do to maintain and grow it? We are a country with a relatively small population, but that doesn’t mean we can’t identify niches and be No. 1 in these areas. We are already an international player in aerospace research, but we can develop a stronger voice.”
Carleton’s aeroNext strategy includes a commitment of $10 million in new funding and a unique partnership with the University of Toronto Institute for Aerospace Studies to establish Carleton as a global hub for aerospace technology.
Leveraging Carleton’s decades-long track record, its faculty and facilities, its multi-disciplinary graduate and undergraduate training programs, and its network of ongoing collaborations with government, industry and other academic institutions, aeroNext’s goal is nothing less than to expand the frontiers of aerospace research.
Canada’s aerospace sector is at a crucial juncture, the federal government’s 2012 review of the industry declares.
“If the sector is to continue to thrive and to benefit the country as a whole, all players — companies, academic and research institutions, unions, and governments — must understand and adapt to changing realities. Success depends on developing the technologies of tomorrow and securing sales in a highly competitive global arena.
“In an international economic environment where change has been breathtakingly rapid, the greatest risks are posed by complacency, and failure to adapt. Inertia would place in jeopardy one of the country’s most important industrial sectors and along with it, the critical economic, technological, and security benefits that flow from a healthy and competitive aerospace sector.”
This is why Carleton University, at the heart of a regional cluster that includes Ottawa’s government enterprise and western Quebec’s industry heavyweights, as well as academic partners in Toronto and around the world, is well-positioned to marshal the momentum that has already been generated and lead the country’s aerospace sector into a bold and promising future.
Wednesday, June 1, 2016 in Aerospace, Engineering, Research
Share: Twitter, Facebook