Lead image by CHUTTERSNAP / Unsplash
By Keroles Riad
This article is republished from The Conversation under a Creative Commons licence. All photos provided by The Conversation from various sources.
Keroles Riad is a postdoctoral research fellow at Carleton University.
Fire is arguably humanity’s earliest discovery. It was pivotal in advancing society — underpinning many of humanity’s most transformative inventions, from cooking and forging weapons to generating energy and enabling car combustion engines.
Today, fire continues to be the gateway to some of the most cutting-edge nanotechnologies currently being developed for use in cancer treatments and as breath sensors for early detection of diabetes and other metabolic diseases.
Nanotechnologies can be found in almost every aspect of our daily lives. For instance, I have previously written about the nanotechnology used in the mRNA vaccines that helped us through the pandemic, and have facilitated conversations discussing how nanotechnology affects our wine, gut and climate.
For example, gas sensors incorporating nanoparticles made via fire can be used to verify that there’s no methanol in alcoholic beverages. Methanol is a highly poisonous alcohol contaminant, and has caused numerous poisonings worldwide.
Fire is how most widely used nanoparticles — and by extension, nanotechnologies — are made. For example, a third of a car tire’s weight is comprised of carbon black nanoparticles, which are made using fire. These nanoparticles help to reinforce the tire. The white paint we use on our walls and the coatings on some pills contain fire-made titania nanoparticles. Similarly, fumed silica — which is used in the optical fibres needed for internet and communication systems — are also forged in fire.
How nanotechnology is made
So how do nanoparticles, which are 80 to 100 thousand times smaller than the thickness of a human hair, form inside a fire?
I specialize in making nanoparticles in fire — specifically using a technology called flame spray pyrolysis.
In my research, I burn flammable chemicals that contain the target metal elements to form my nanoparticles. Everything gets oxidized during combustion: carbon becomes CO2, hydrogen becomes water vapor and metal elements become metal oxides.
During the milliseconds that these metal oxide particulates spend inside the fire, they collide and grow into nano- or micro-particles. I collect these particles on a filter on top of the fire. Important properties such as the size and crystal structure of the nanoparticles that are produced depend on how much time these particles spend inside the fire.
The more time the particles have to collide inside the forging fire, the larger they grow. We can also make complicated particles consisting of multiple elements by burning a mixture of different chemicals. This process is both versatile and scalable — allowing millions of tonnes of nanoparticles to be produced each year.
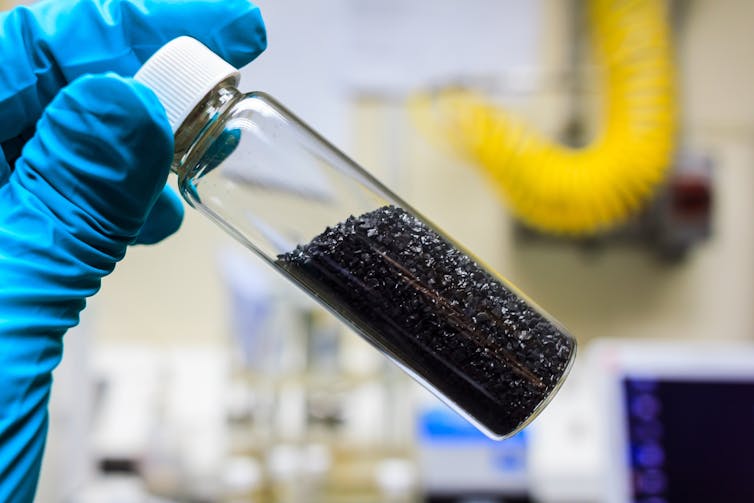
(Shutterstock)
Overcoming limitations
Being able to mass-produce nanoparticles has been one of the biggest challenges of producing nanotechnologies on a larger scale. This is because most of the nanoparticles used in nanotechnologies can only be made via “wet chemistry,” or by using liquids.
It can take hours of working with liquid in beakers, mixing them, heating them, then separating and centrifuging them just to obtain tiny amounts of material. These processes are often too expensive and too dangerous to scale enough for viable commercialisation.
For instance, quantum dots (nanoparticles made from semiconducting materials which have both optical and electrical properties) — the discovery of which was celebrated by the Chemistry Noble Prize in 2023. These have the potential to revolutionize many technologies — including solar cells, carbon capture and contrast agents used in medical imaging.
However, quantum dots are hardly ever used in those technologies on a large scale because the prohibitive cost of making them via wet chemistry can be as high as US$45,000 per gram.
But unlike wet chemistry, fire is simple, cheap, scaleable and surprisingly safe. So when processes that allow for the production of high value nanoparticles, such as quantum dots, with fire are developed, costs drastically drop and they become immediately scaleable and of potential interest to industry.
Fire can also produce harmful particles and by-products.
For instance, if you place a napkin in front of the exhaust of your car, black stuff will accumulate on it. This black residue is soot particles produced by the fire burning inside the engine. Similarly, smoking cigarettes causes soot to form and accumulate in a smoker’s lung, often causing cancer.
Soot is also, by some estimations, the third highest contributor to global warming after carbon dioxide and methane. However, those assessments may actually be underestimating the true contribution of soot to greenhouse gas effects.
Flame spray pyrolysis technology has also been used to simulate combustion conditions to not only study the impact of generated soot more accurately, but also test process changes that could virtually eliminate soot emissions. For example, one study used flame spray pyrolysis to show that injecting air downstream of jet fuel combustion can reduce soot emission by more than 90 per cent. Flame spray pyrolysis could continue to be a useful tool in researching the impacts of pollution.
The future of nanoparticles
But not all nanoparticles can be produced by fire. As such, research exploring new recipes and processes to make high-value nanoparticles that are not yet possible to make in fire could have a large impact.
For example, a major focus of my current work is to explore the possibility of using fire to make graphene. Graphene is the strongest material known at the nanoscale. My previous work shows that by using ultraviolet light, graphene can be transformed into strong macroscopic structures — possibly allowing it to be used in 3D printing.

(Shutterstock)
Further, there’s massive untapped potential in nanomedicine to integrate the nanoparticles that are already possible to make in fire. Only about 30 types of nanoparticles are approved by the U.S. Food and Drug Administration — such as those used in COVID-19 vaccines, as well as iron-based nanoparticles used for treating anemia and kidney disease.
All those approved nanomedicines are given via injections. This leaves plenty of room to explore the benefits of inorganic nanoparticles in medicine — especially orally administrated therapeutics.
Thursday, May 1, 2025 in The Conversation
Share: Twitter, Facebook