By Dan Rubinstein
Photos by Terence Ho
When somebody sips a frosty pint of beer, they might briefly reflect on the ingredients in the glass — a timeless blend of grains, hops, yeast and water — but they probably don’t think about the byproducts from the brewing process. Unless they have the mind of an engineer.
Before moving to Canada for graduate school, Seyedomid Ahmadinejad designed residential and industrial wastewater treatment systems in Iran. He knew that after water and tea, beer is the third most popular drink around the world, and that by volume, brewing can produce up to ten times more wastewater than beer — a brownish, earthy smelling liquid that contains elements such as nitrogen and phosphorus, as well as traces of the chemicals that breweries use to clean their tanks and lines.
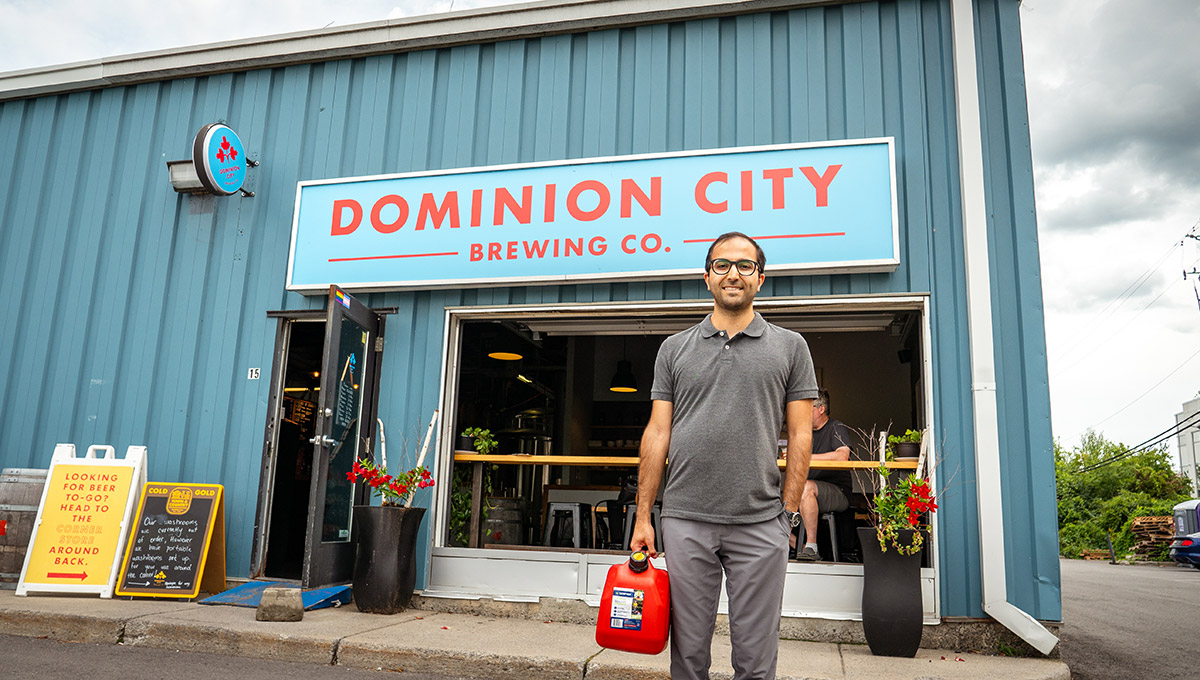
Carleton University grad student Seyedomid Ahmadinejad
So when Ahmadinejad had to choose a focus for his master’s degree in environmental engineering at Carleton University, one particular research project jumped out. What if he could devise a way to help breweries not only avoid the expensive, energy-intensive process of sending their wastewater into municipal sewer systems, but also convert that effluent into a product that’s good for both the environment and the bottom line?
“We’re turning brewery wastewater into renewable energy,” says Ahmadinejad, who is using his lab at Carleton to treat samples supplied by Ottawa’s Dominion City Brewing Co., producing a biogas that could be used to generate electricity, heat buildings, fuel vehicles — or, potentially, to power on-site brewing operations.
“I wanted to come up with a solution to one of the big challenges that the brewing industry faces and help make their business more sustainable.”
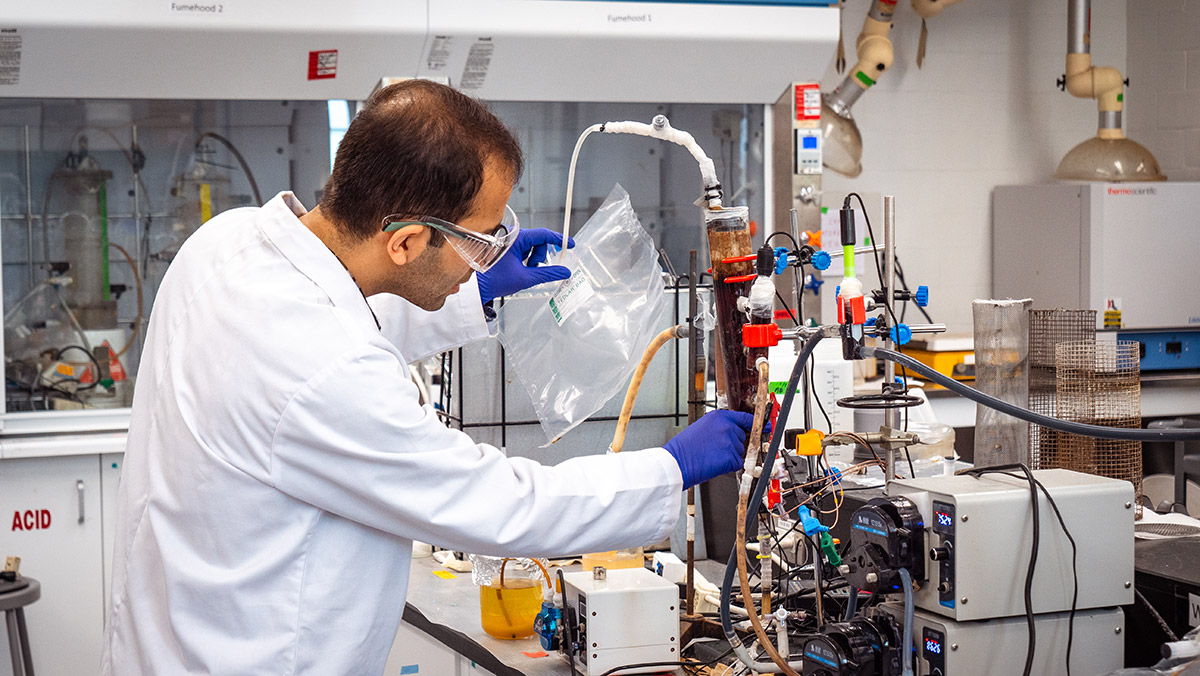
Energy Intensive Wastewater Treatment
In Iran, Ahmadinejad observed the significant energy requirements of conventional wastewater treatment processes, a series of steps to filter and disinfect the wastewater, removing substances that can have detrimental effects if released into the environment.
Rather than using energy to treat wastewater, he is advancing a new technology called bioelectrochemically enhanced anaerobic digestion, or BEAD, to maximize energy recovery from brewery wastewater.
Under the supervision of Carleton professors Abid Hussain and Banu Örmeci, Ahmadinejad has developed a prototype BEAD system containing several non-pathogenic microorganisms. He “feeds” brewery wastewater into this oxygen-less system and the microorganisms boost traditional anaerobic digestion, a microbial process that breaks down organic material in waste to produce biogas.
The methane composition of biogas produced by anaerobic digestion is typically around 50 per cent, but BEAD’s enhancements, which include quicker reaction rates and a more stable process, have increased that to 80 per cent. The higher the percentage, the more viable the biogas will be.
Ahmadinejad has been developing this system for the past two years, monitoring it almost daily and making small adjustments. “We’re constantly revising our method to get a different result,” he says. “Every day is a new challenge.”
For this research to be effective, Ahmadinejad needs genuine brewery wastewater. For his first master’s degree, he worked on a way to remove pollutants from a synthetic leachate, which is fine for the lab but not always transferable to the real world.
“Real wastewater can have slightly different characteristics each time you treat it,” he explains.
“You need to develop a method that can handle these differences.”
Seeking a collaborator, Ahmadinejad approached several Ottawa breweries. Dominion City was the only one that replied.
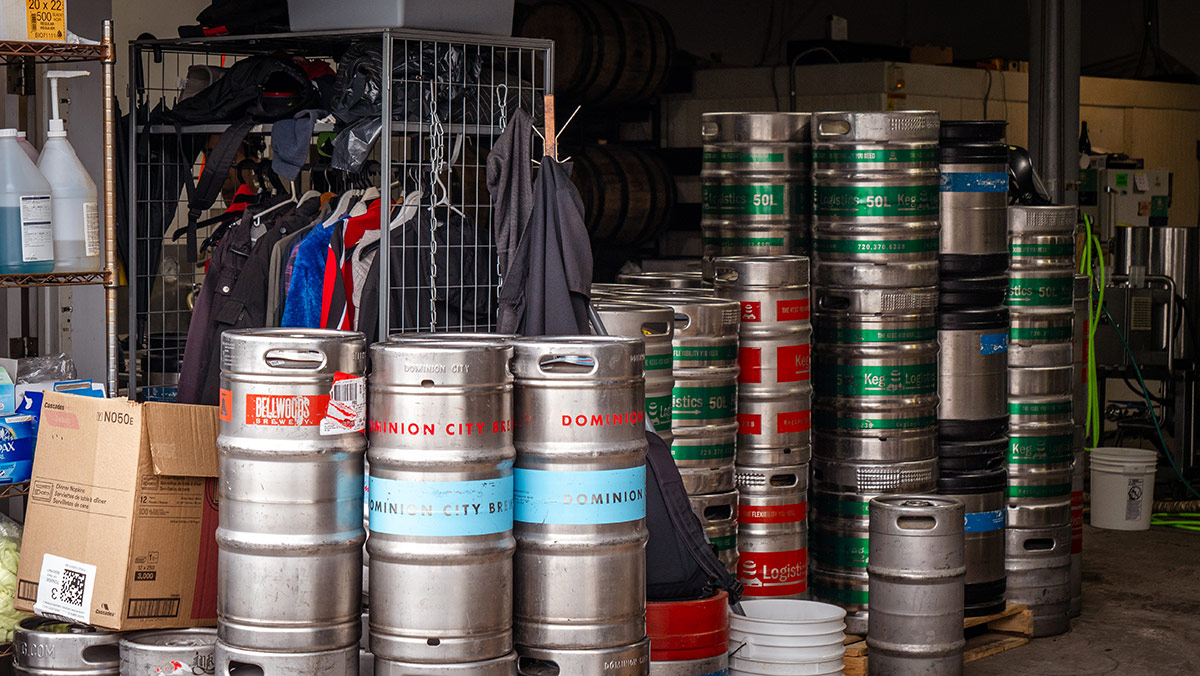
Giving Back to the Community
Launched in 2014 by a trio of Carleton graduates, including current owner Josh McJannett, Dominion City is driven by a desire to give back to the community alongside selling beer.
It has raised money to help resettle refugees, relies on local suppliers and established a scholarship to make the brewing industry more diverse.
“A big part of our company’s mission is to be involved in the community,” says head brewer and operations manager Scott Denyer.
“Whether it’s through charity work or sponsorships, we’re always looking to be engaged.”
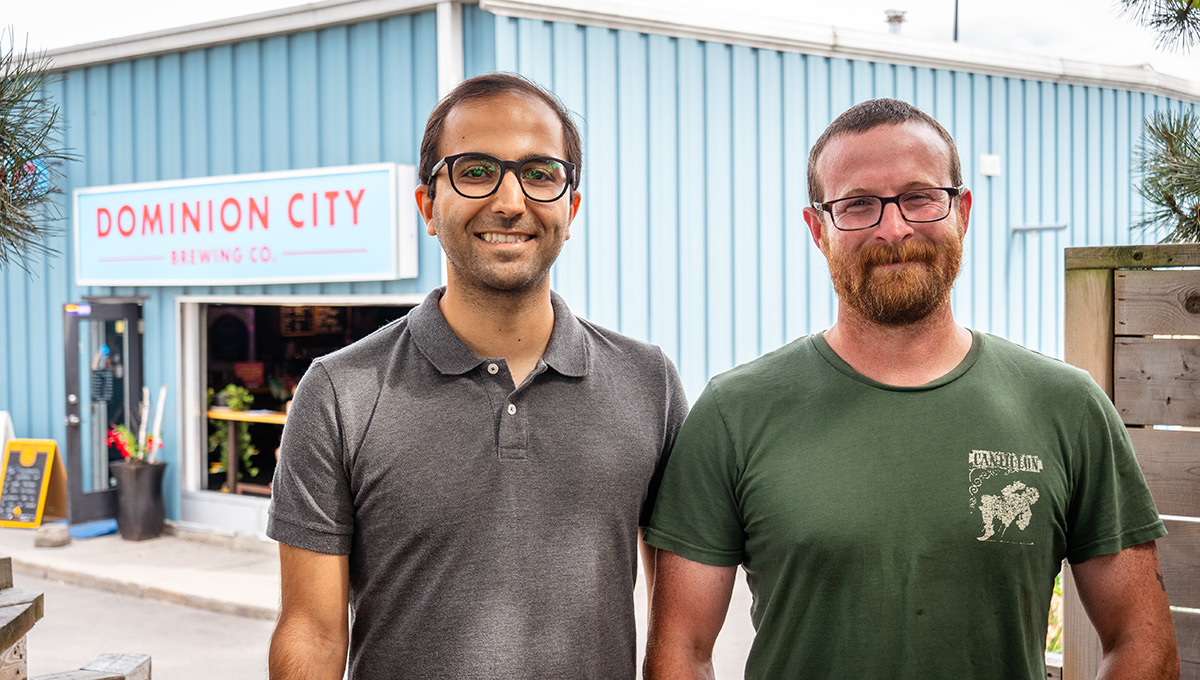
Ahmadinejad and Dominion City head brewer and operations manager Scott Denyer
Every couple months, Ahmadinejad goes to the brewery, which is located in an east-end industrial park, with two or three 20-litre jerry cans. Denyer fills the bright red containers with wastewater from a 3,000-litre effluent tank and Ahmadinejad brings the sample back to his lab.
Dominion City brews about 5,000 hectolitres of beer a year, producing anywhere from 3,000 to 6,000 litres of wastewater every day. “That’s a lot of byproduct that needs to be side streamed,” says Denyer.
Typically, the wastewater is collected in a tank, which helps separate solids like yeast, hops and other organics. These go into the compost, which Dominion City pays to have removed, while the remaining wastewater, containing chemical cleaning byproducts, because the company has to be extremely sanitary, is discharged into the municipal sewer system, which also incurs a fee. These costs add up to thousands of dollars every month.
“We’re happy to be part of projects like this because they could help us reduce our expenses and are good for the industry overall,” Denyer says about participating in Ahmadinejad’s research.
“There’s always potential for these things to grow into something meaningful. Brewing beer is a difficult business to make money in, so anything we can do to cut our costs while being environmentally friendly is a big win.”
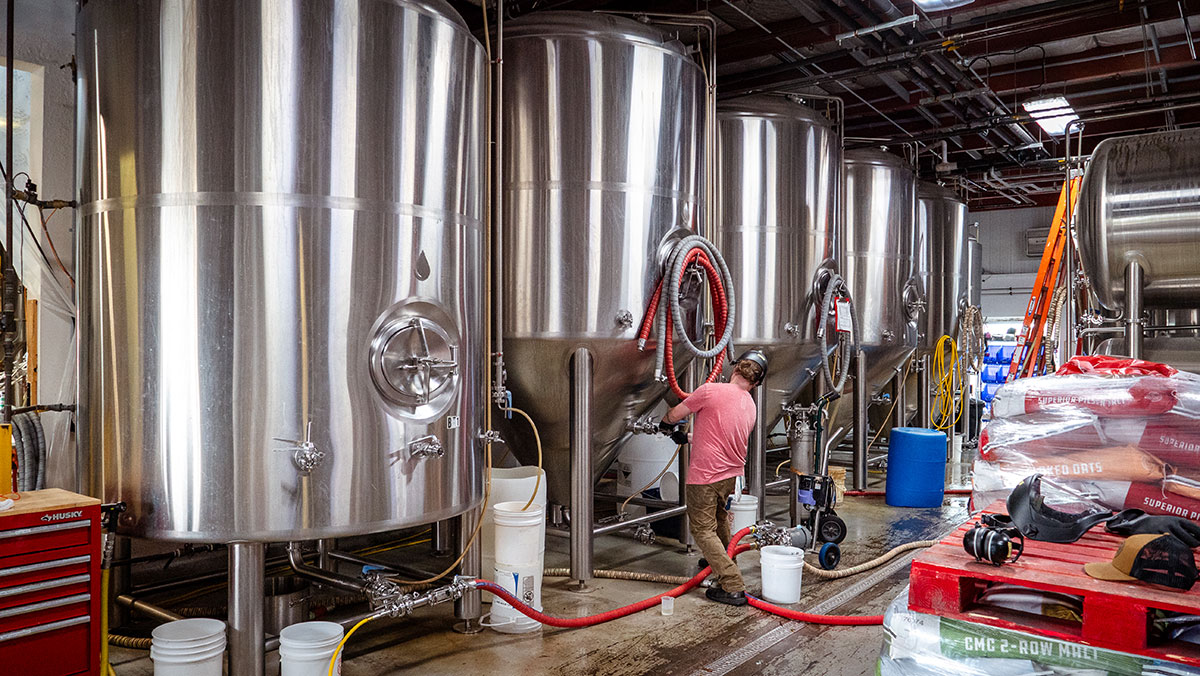
Wednesday, September 4, 2024 in Alumni, Faculty of Engineering and Design, Grad Stories, Research
Share: Twitter, Facebook