By Dan Rubinstein
Last spring, in a parking lot on the National Research Council campus in east Ottawa, a team of students from Carleton’s Department of Mechanical and Aerospace Engineering simulated a rear impact collision between a car and a cyclist.
Working in partnership with the Ottawa Police Service, the 20 fourth-year students recorded data such as head and chest acceleration from an instrumented crash test dummy they had developed, seeking a better understanding of the injuries that occur as part of a broader initiative to improve bicycling safety.
The accident simulation, which involved designing components of the dummy to mimic human properties and installing sensors to accurately gather crash data, as well as the use of calibrated video cameras to reconstruct the impact dynamics in 3D, was one of the final stages of their capstone project — a design exercise that every engineering, architecture, industrial design and information technology student in the Faculty of Engineering and Design (FED) must complete in their final year.
These collaborative projects, a hallmark of an engineering education at Carleton, were introduced to the Mechanical and Aerospace Department in 1991, when the first cohort of Bachelor of Aerospace students entered their fourth year, and subsequently expanded across the research-intensive faculty. And over the past quarter-century, many of the student efforts, such as an uninhabited aerial vehicle (UAV) for high-resolution geomatic surveys, have led to real-world innovations.
“Our capstone engineering design projects are one of the many ways that Carleton integrates real-world experience into its programs,” says Rafik Goubran, acting vice-president (Research and International). “We have the privilege of witnessing a continuous influx of innovations and are constantly impressed by the calibre and scope of the ideas that come from our students.”
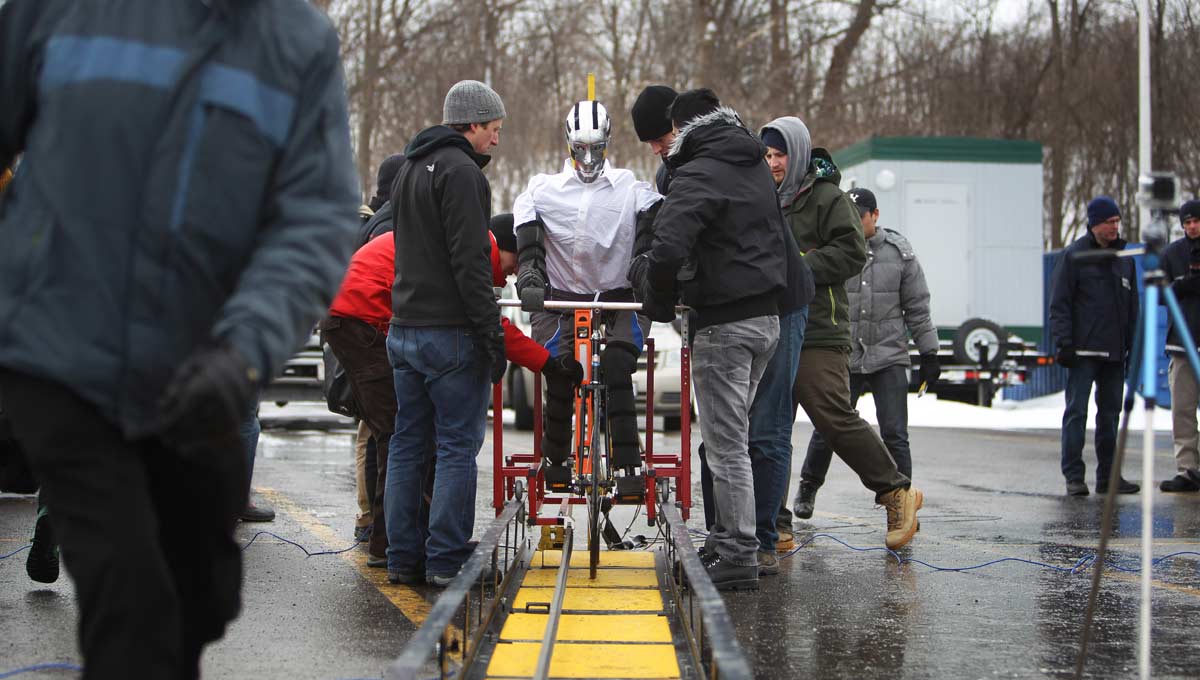
Engineering students team
up to innovate
Engineering students at Carleton do hands-on design work throughout their undergraduate degrees. In fourth year, under the leadership of faculty supervisors, they’re required to produce an original design innovation, working in teams with anywhere from three members to massive multi-disciplinary groups of up to three dozen or so students.
This approach is extremely valuable because it teaches teamwork and reflects the way things are done by industry, says Prof. Jeremy Laliberté, the capstone co-ordinator for the Department of Mechanical and Aerospace Engineering.
“Capstone projects help students develop communication and problem-solving skills,” he says. “They deal with conflicts, disagreements, changing priorities and limited resources — all of which professional engineers regularly have to contend with.
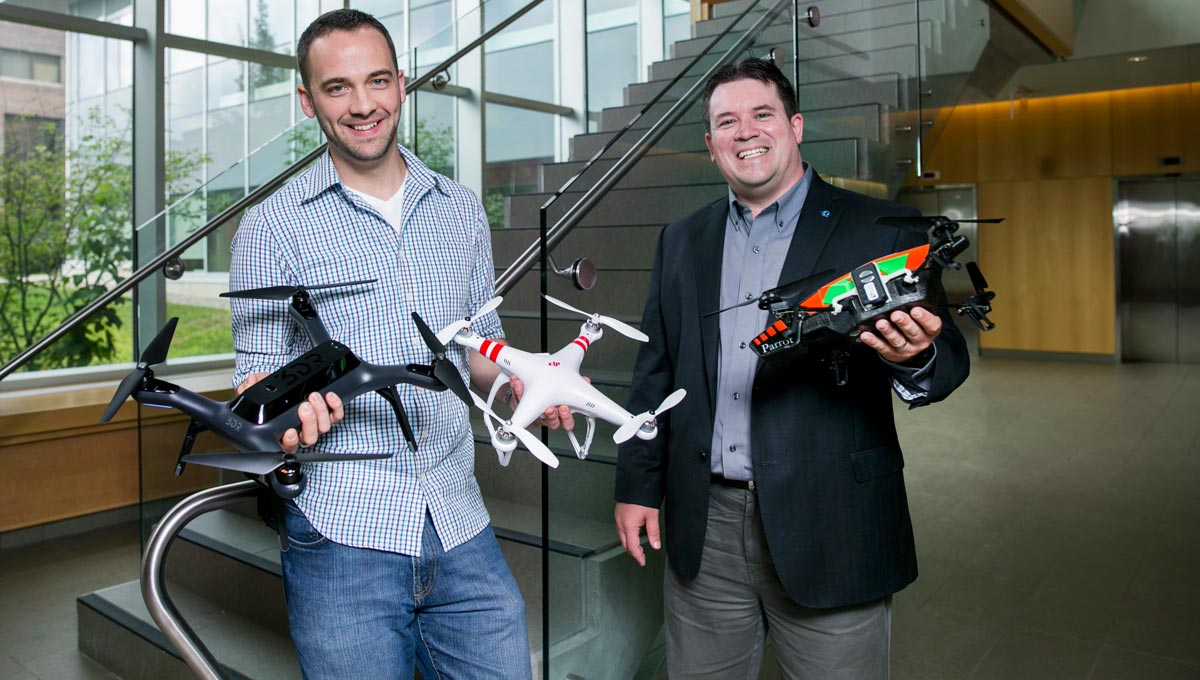
Jeremy Laliberté (right), director of Carleton Aerospace and associate professor<br /> in the Department of Mechanical and Aerospace Engineering
“There’s no solution manual, no pre-set answers. That’s one of the challenges. Students really have to strike out on their own, and put time and energy into their projects. We make sure they understand that they have ownership, which sets them up for the real world.”
Writing and presentations are also part of the process — important tools for engineers when they must convey the results of their work to colleagues and external audiences.
Laliberté, who started his undergraduate degree at Carleton in 1992, was part of the structural group for his capstone, a business jet design project, in 1996-‘97.
“I lapped it up,” he says. “It was the first time we really got to apply the knowledge we had learned into making an aircraft.
“I spent way more time on this than I probably should have. My group took it very seriously — there were a few all-nighters on campus.”
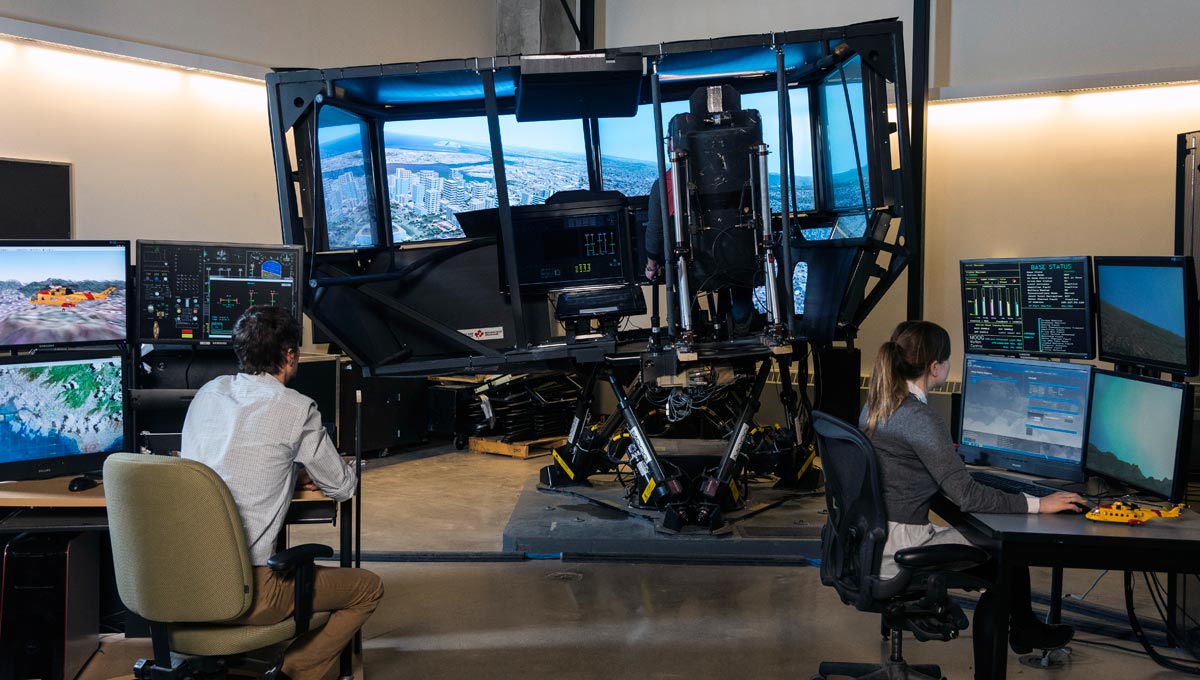
Carleton sets the standard in Canada
Aircraft and spacecraft projects were the first two aerospace capstones when the projects were introduced to the Department of Mechanical and Aerospace Engineering 25 years ago, based on a model developed at Cranfield University in the United Kingdom.
At the time, Carleton was the only university in Canada with team-style projects — an approach that was soon adopted throughout the department and emulated at other schools, such as Ryerson and Royal Military College.
The original two mechanical and aerospace projects have evolved into nine options, among them spacecraft, fixed-wing and rotary-wing UAVs, high-performance housing, and a hybrid natural gas vehicle. And what were once year-long largely paper exercises are now frequently multi-year efforts that involve building working models, such as the Carleton University Simulator Project (CUSP), a state-of-the-art spherical flight simulator, the only one of its kind in Canada.
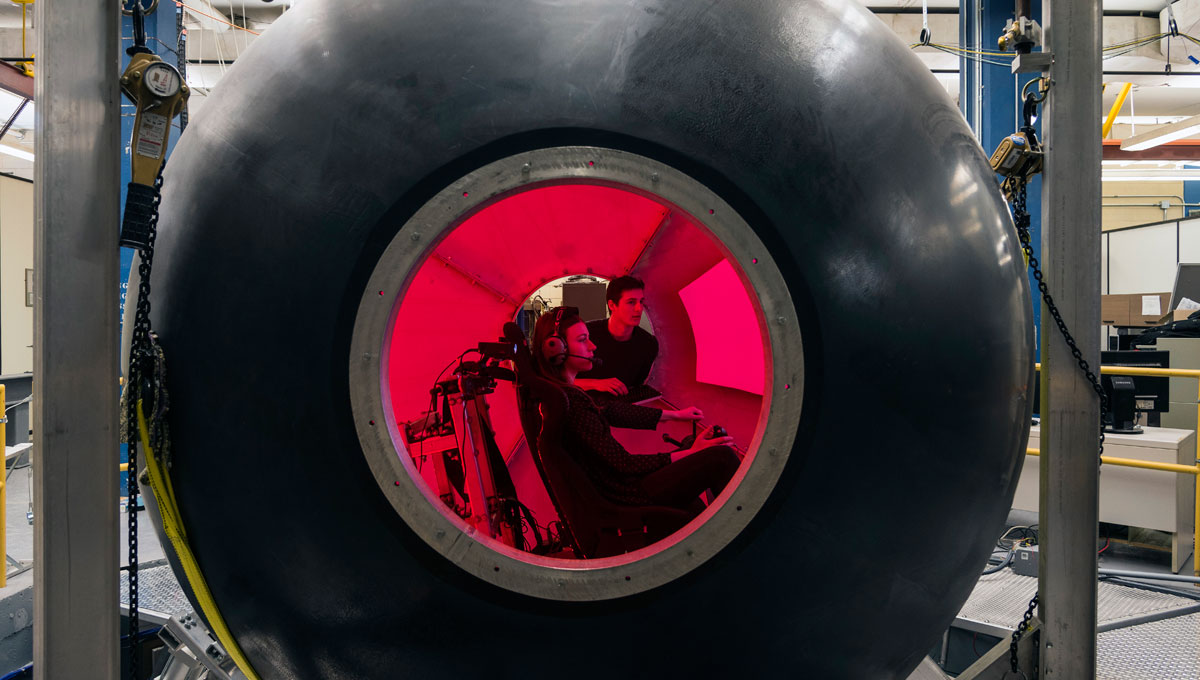
The Carleton University Simulator Project (CUSP), a state-of-the-art<br />spherical flight simulator,the only one of its kind in Canada.
Students must satisfy a review from government and industry experts at the end of the capstone, and then in some cases hand over their project to the next year’s group, a transition that highlights the importance of detailed documentation and project management.
They also cross disciplinary lines. Students working on the flight simulator project, for example, come mostly from the departments of Mechanical and Aerospace Engineering, and Systems and Computer Engineering.
A recent success was Carleton’s Blackbird UAV team, which won an innovation prize at the 2016 Unmanned Aerial Systems Student Competition in Manitoba last spring. Students were required to fly a UAV over a field in order to examine the health of a farmer’s crop. Each team was asked to measure soil conditions and map the location of the crops using a sensor system.
Other recent projects have included a prosthetic hand built using 3D printing technology, an advanced radon detector for real-time continuous home monitoring, residential home designs that optimize advanced solar power techniques, and a biometric scanner that combines standard fingerprint scanning with electrocardiography.
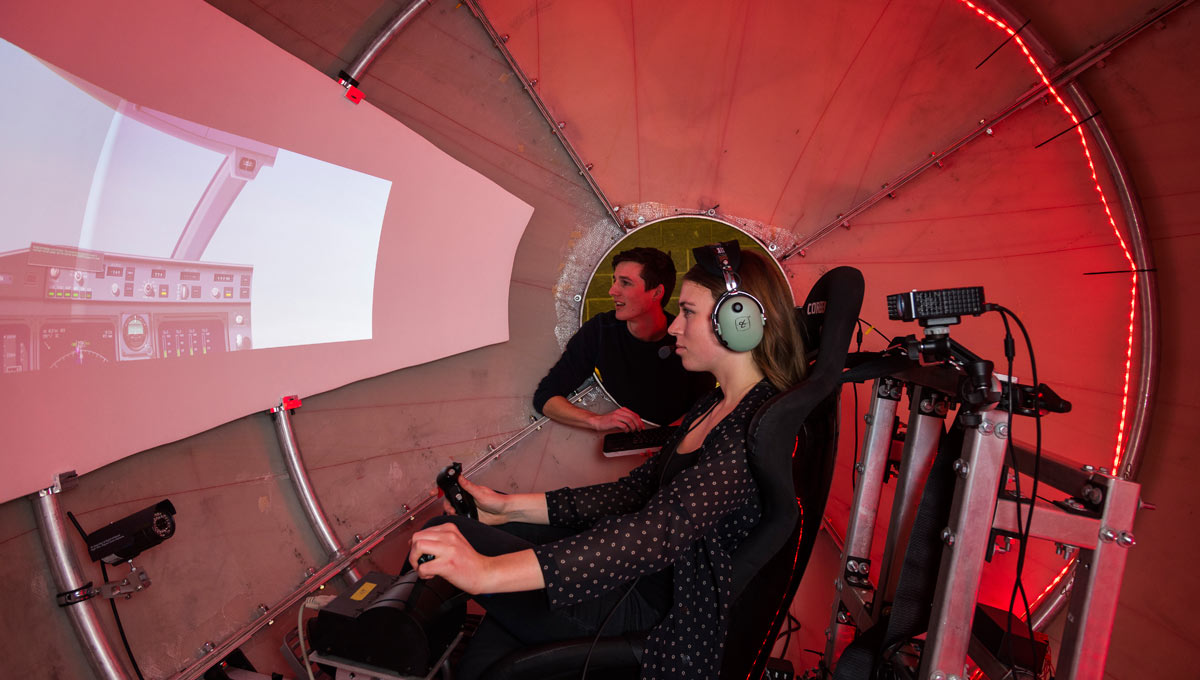
Capstones replicate the “real world”
When he was an undergraduate engineering student at Carleton in the early 1990s, Robert Mobilio, Bombardier’s director of in-service engineering and the company’s CRJ and Q Series Customer Response Centre, worked on a capstone that came up with the preliminary conceptual design for a small aircraft.
On a team with 15 others, he helped design the landing gear, but what stands out from the experience was how it taught him to collaborate and truly understand how his area fit into the project as a whole.
“Until I got into the workforce, I didn’t fully appreciate how similar the capstone project was to how things work in the real world,” says Mobilio, who began his career as a stress engineer and now leads a team of 165 people that does repairs, troubleshooting support and systems engineering on the company’s CRJ and Q Series aircraft platforms.
“It helped me tremendously when I started at Bombardier. I understood aircraft and how they fly, and how to speak the right language so I could communicate with people in different departments.”
Tim Smith, MDS Aero Support Corporation’s director, mechanical engineering, worked on the CUSP capstone in its first year, 2001. He chose that project from five options because it was brand new.
“The learning curve was very steep,” says Smith, noting the capstone’s emphasis on how to work within a team. “It was interesting to hear and have to mesh with other people’s perspectives on how to do things.
“When you’re studying, it’s your pace and style. But when you need to deliver on deadline as a team, you have to look at things in a different light.”
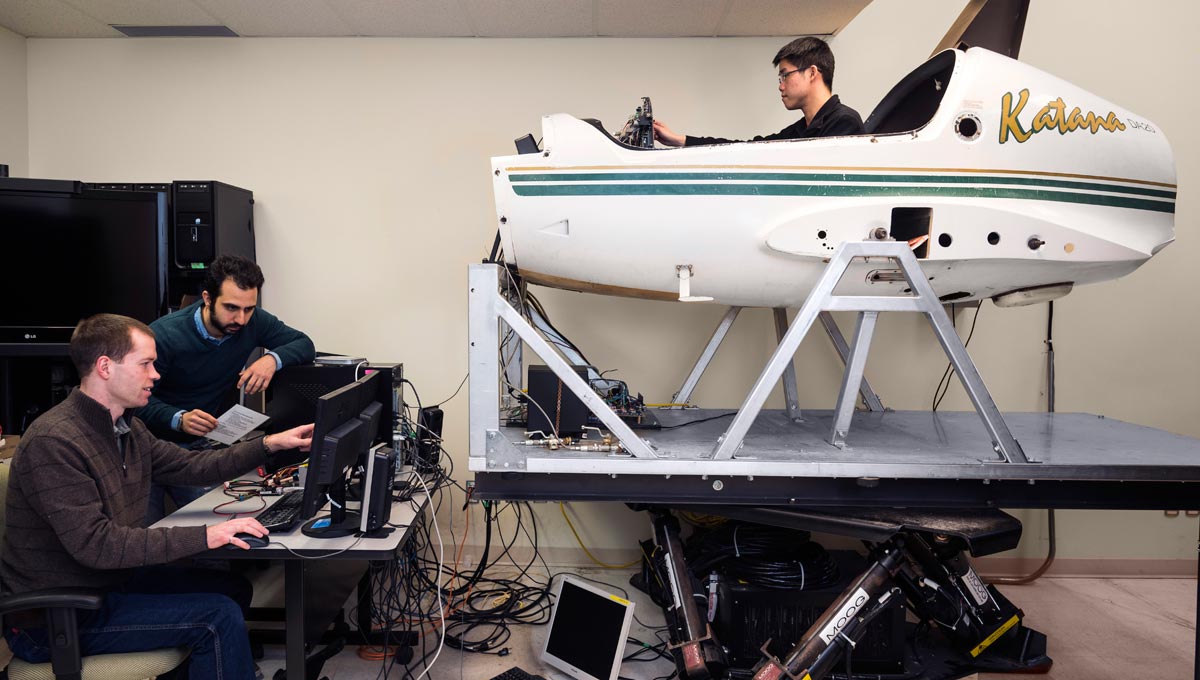
Friday, October 28, 2016 in Aerospace, Engineering, Research
Share: Twitter, Facebook