By Jena Lynde-Smith
Photos by Brenna Mackay
In Canada, about 13.7 per cent of individuals aged 15 and over report having mobility disabilities, requiring the use of assistive devices such as canes and wheelchairs to walk or climb stairs. Despite their widespread use, these traditional tools have limitations as they can cause physical strain, restrict terrain navigation, and pose daily accessibility challenges.
To address these issues, Carleton University researcher Mojtaba Ahmadi is designing advanced exoskeletons – wearable robotic devices powered by artificial intelligence (AI). These exoskeletons aim to provide assistive force for walking and daily activities while addressing the limitations of traditional assistive devices – offering improved mobility and accessibility for individuals with disabilities in Canada and beyond.
“Exoskeletons can help people stand up and walk, they can help with posture,” says Ahmadi, a professor in Carleton’s Department of Mechanical and Aerospace Engineering. “If the device is strong and smart enough, it’s an excellent way for people with disabilities to regain function and autonomy.”
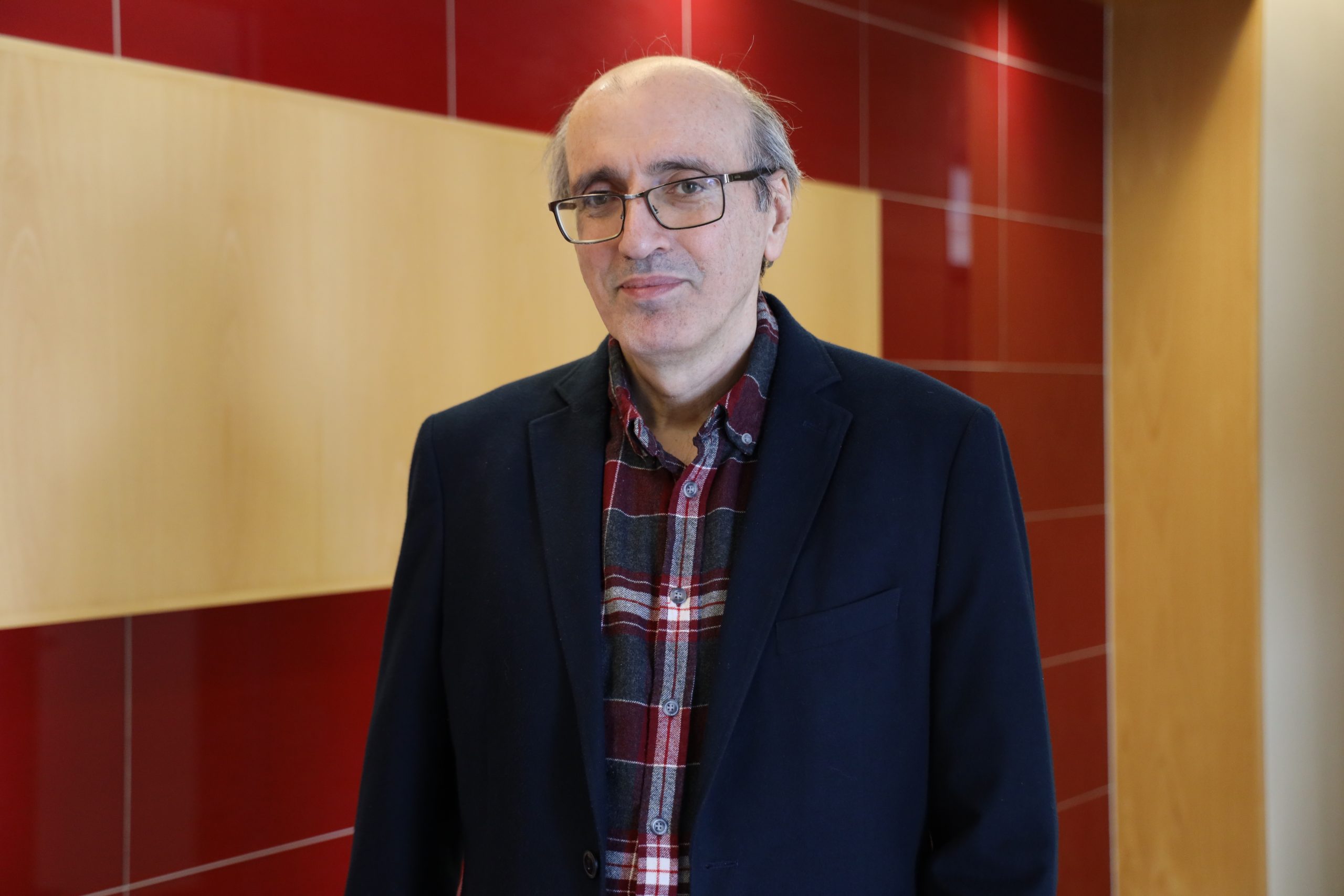
Mojtaba Ahmadi, Carleton University mechanical engineering professor
Advancing Traditional Exoskeletons with AI
Robotic exoskeletons emerged in the 1960s, primarily for military and industrial uses. It wasn’t until the late 2000s that significant advancements were made, leading to their development for medical and rehabilitation purposes.
Despite their improvements, many exoskeletons still do not adapt well to the user’s intentions, leading to awkward or inefficient movements. This can result in injury or accidents if the exoskeleton applies too much force or moves in an unexpected way.
In Carleton’s Advanced Biomechatronics & Locomotion (ABL) lab, Ahmadi and his research team are programming the next generation of robotic exoskeletons using AI so that they seamlessly cooperate with users.
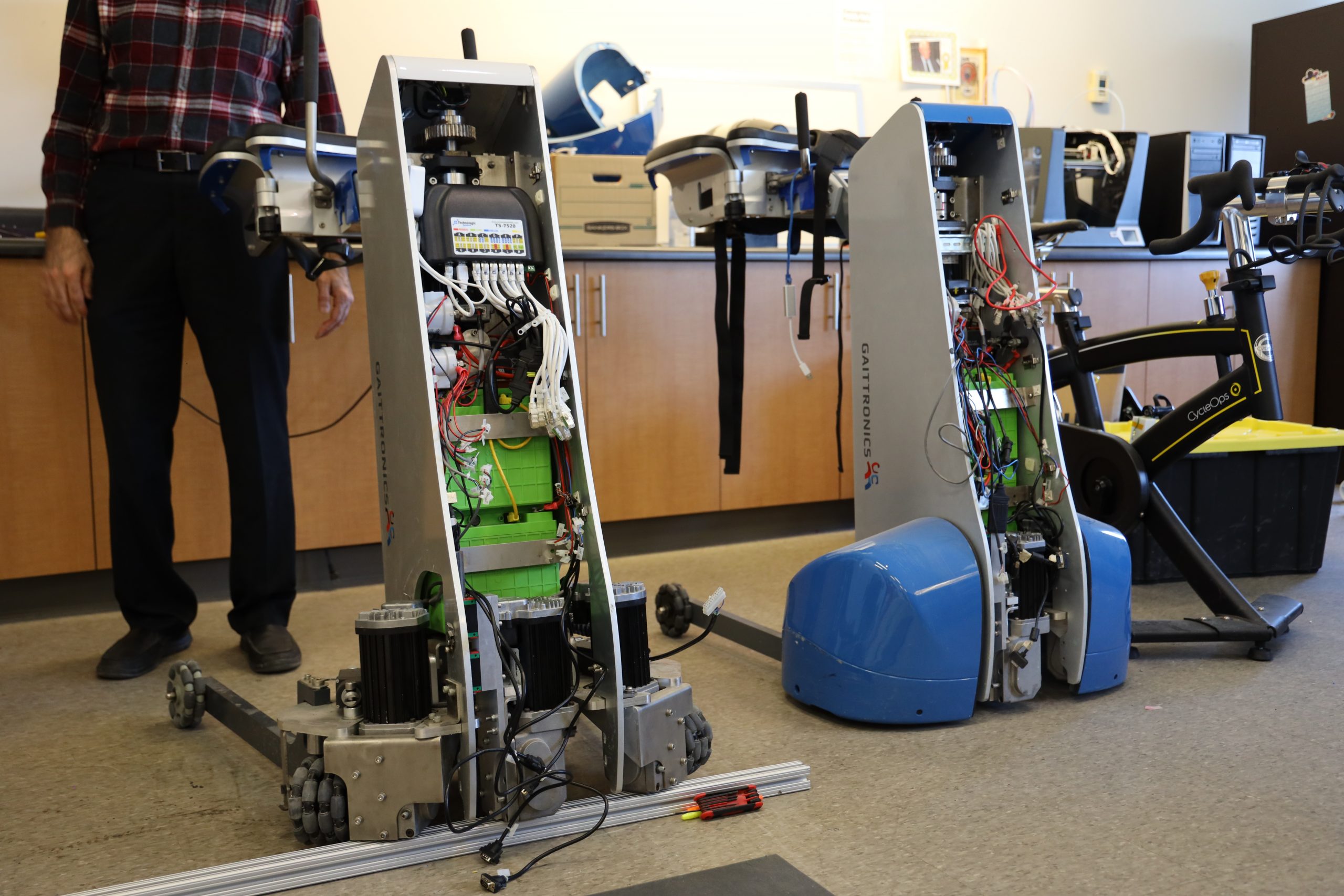
A prototype of a walking device built in the ABL lab
“The objective is to try and develop controllers based on body signals that would require the least amount of pre-planning,” Ahmadi explains.
“The robot uses machine learning to detect the load you are carrying, predict what you are doing, and adapt to helping you with the task.”
To achieve this level of machine intelligence, Ahmadi’s team is using sensor technology to gather data about individual’s movements. This involves attaching electrode sensors to a person’s skin over various muscles and having them perform every-day tasks.
The sensors detect and record the user’s movements by picking up small voltages and categorizing them with a specific task. Using the data collection from this stage, Ahmadi’s team can program the exoskeleton to understand what a person’s movements mean.
“We have to ensure that the robot helps the user but not too much,” Ahmadi explains.
“For someone who has a bit of function or strength, it’s not a good idea to provide all the effort that is needed to perform a task. Otherwise, muscles and bones start the to get smaller and weaker.”
This delicate balance is what Ahmadi refers to as regulated assistance.
“Everyone’s bodily cues are different,” he says. “Exoskeletons should be tailored to meet each user’s unique needs.”
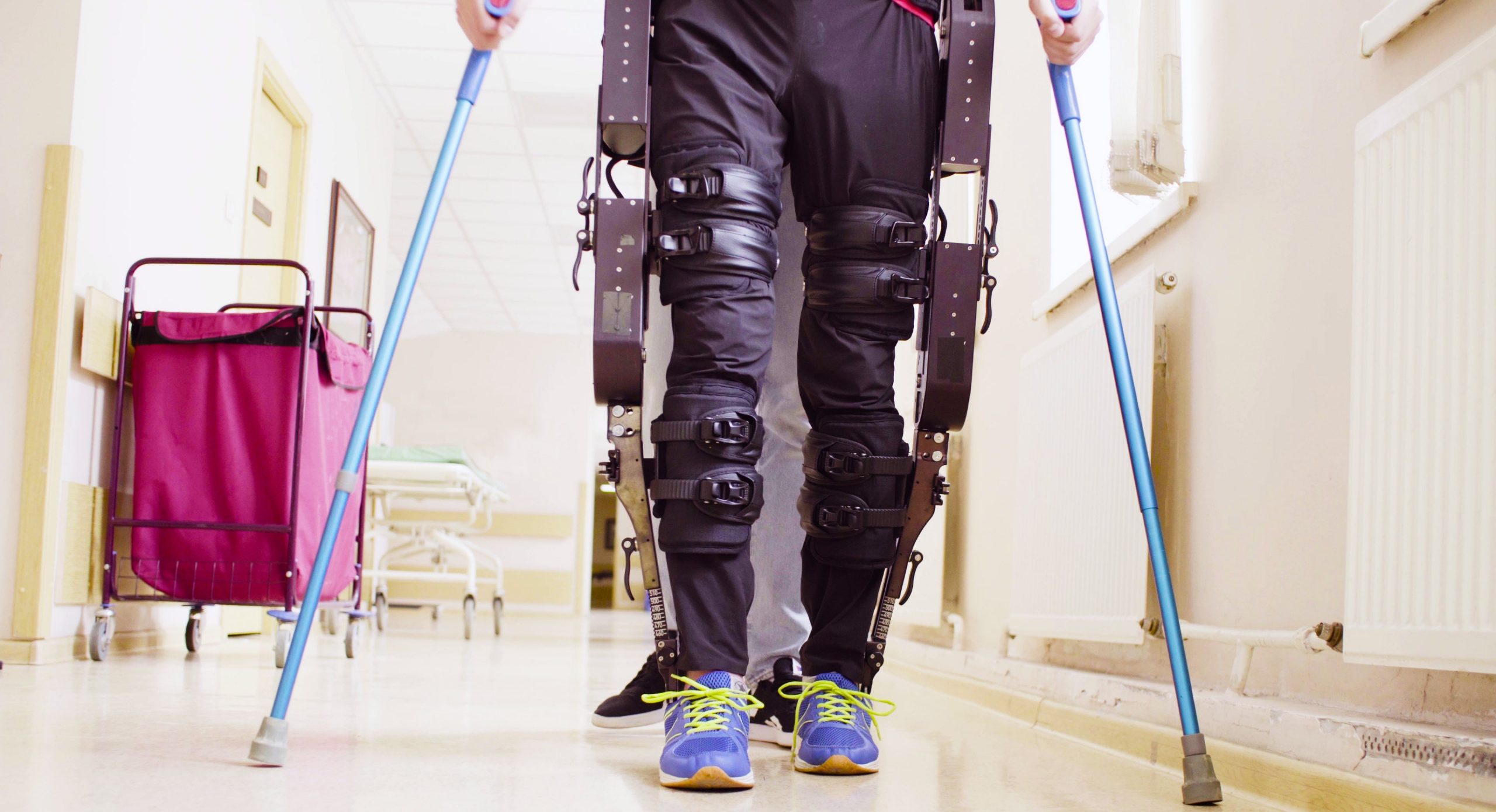
Building an Exoskeleton for Assistive Walking
In the lab, Ahmadi’s research not only centers on addressing the significant challenges with current-day exoskeletons but also offers invaluable experiential learning opportunities for students.
Ahmadi’s Intelligent Telepresence Assistive Devices (iTAD) capstone project brings together 16 fourth-year engineering students in the development of robots tailored for assistive mobility. Currently, their focus is on designing a light exoskeleton assistive walking device – which they named EAWa.
“The goal is to increase accessibility to those living with walking disabilities and to help healthcare workers support their patients more easily and efficiently,” says Ahmadi.
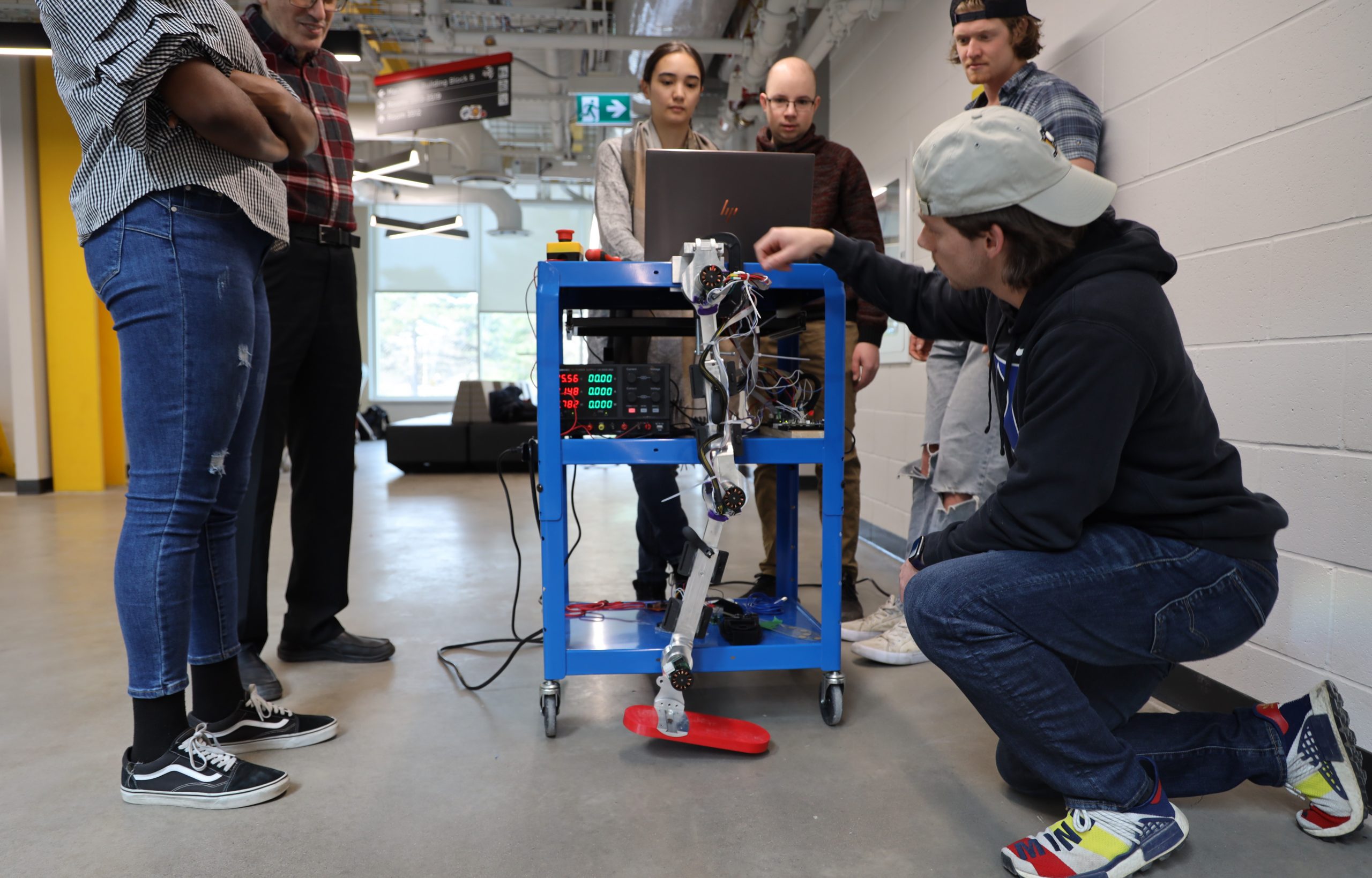
Mechanical engineering students are building an exoskeleton for assistive walking, named the EAWa
The EAWa – which is worn around the legs, hips and feet – is made of mostly as aluminum and 3D printed materials, making it lightweight and easy to use. Equipped with motors and sensors, the device will eventually utilize the similar machine learning technologies used in Carleton’s ABL Lab.
“If the wearer is having difficulty lifting their leg to take a step, the exoskeleton will provide assistance by lifting the leg for them,” Ahmadi explains.
“Similarly, if the user is having difficulty maintaining balance, it will provide support to help them stay upright.”
The device is part of a three-year project. In its first year, students focused on the design aspects and began building the prototype. This year, a different cohort stepped in to continue its construction and implement its base controllers and programming. The plan is for the third and final group of students to run tests, fine-tune, and complete the device next year.

Prof. Ahmadi and five members of this year’s iTAD team: Rory Butterfield, Oghenemega Idolor, Jessica Taylor, Quinn Lee-Ward and Erik Webster
By 2026, Ahmadi hopes to begin running clinical trials with the exoskeleton at the Ottawa Hospital.
“There are few more challenging, or rewarding, design problems than augmenting the human body,” says Quinn Lee-Ward, this year’s student mechanical engineering lead for the project. “Working with the iTAD team was a rewarding experience that challenged my ability to blend practical engineering with creative, thoughtful, design solutions.”
Disability Research Fueled by Personal Experiences
Ahmadi’s initial interest in helping people with disabilities stemmed from wanting to help family members with physical ailments.
“I know it can be isolating,” he says.
“When I was a kid my grandfather had a stroke, he was in bed lying down for two years before he passed away. I saw how debilitating it was. I also witnessed meningitis take away my father-in-law’s balance.”
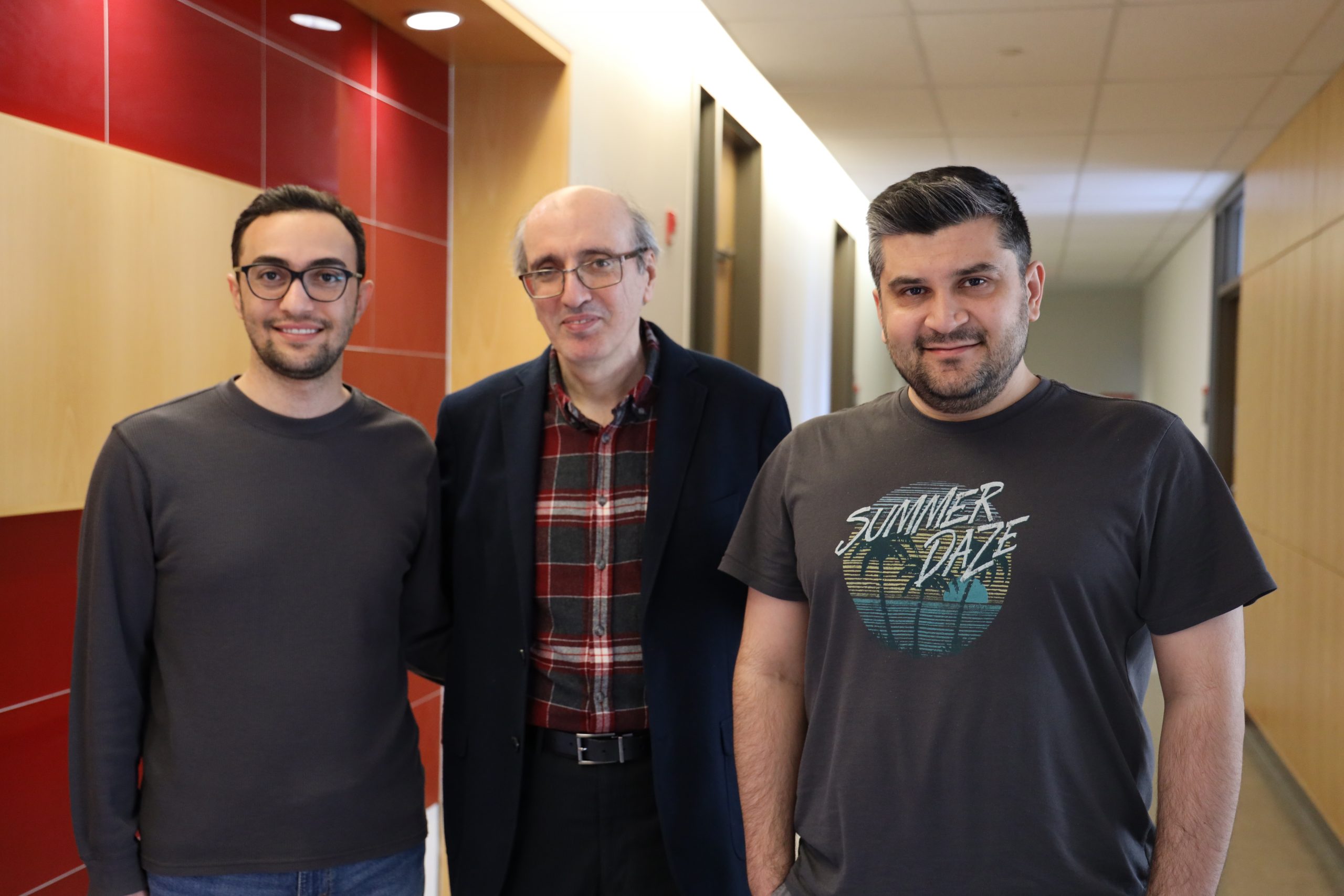
Mojtaba Ahmadi (center) and two PhD students from his lab, Sayyed Hossein Sadat Hosseini (right) and Masoud Karimi (left)
Now in the thick of his work, Ahmadi is motivated by the growing number of people living with physical disabilities in Canada.
“After you start working on medical side of things and talk to your colleagues in the hospital, you learn about challenges that people have.”
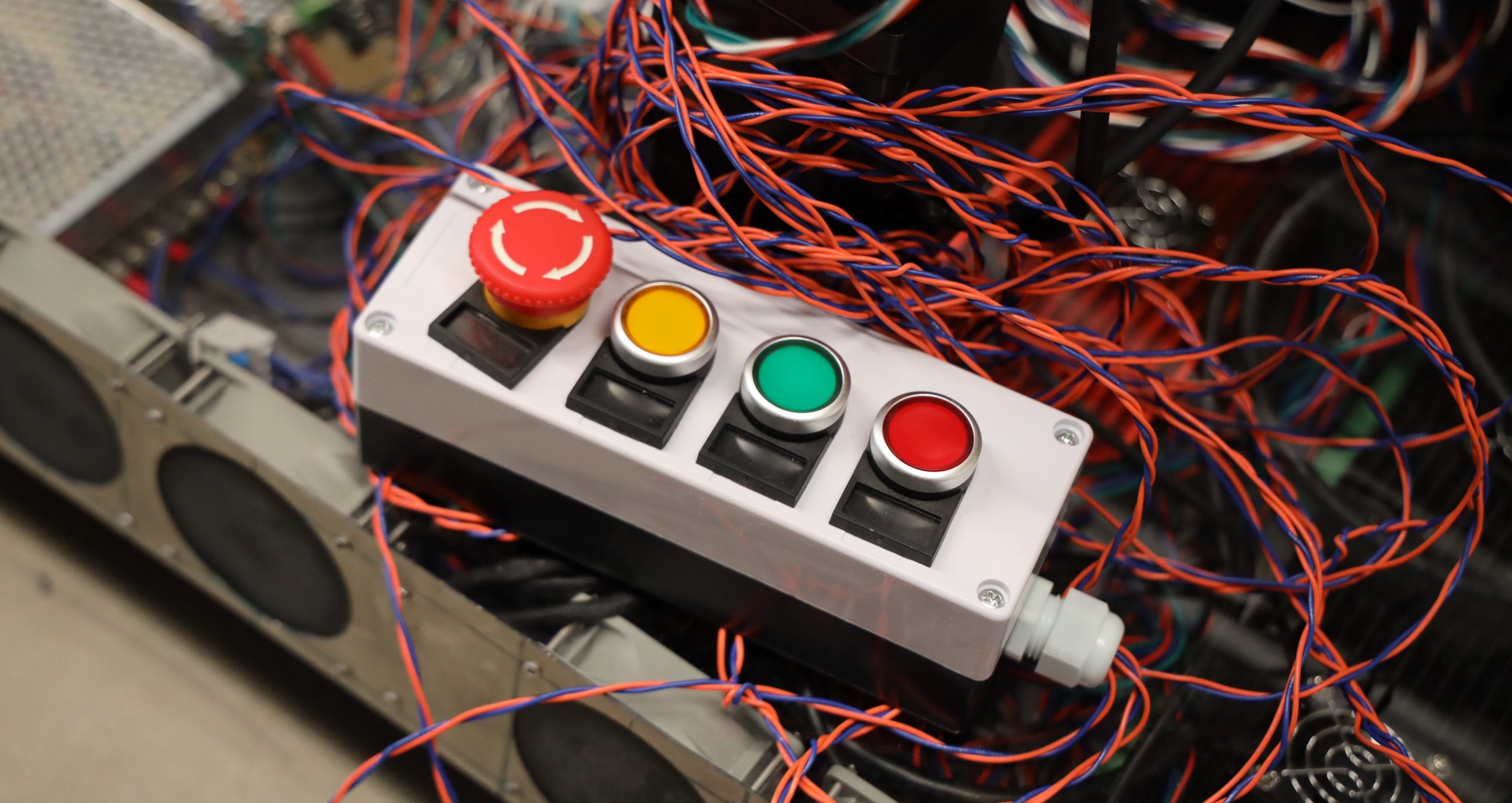
Thursday, April 11, 2024 in Accessibility, Artificial Intelligence (AI), Engineering, Experiential Learning
Share: Twitter, Facebook