By Dan Rubinstein
Photos by Justin Tang
It was the best late Christmas present ever for Joana Rocha.
In early January, after a couple years of design work, correspondence, fabrication, installation and calibration, Carleton’s new Aeroacoustics Testing Laboratory in the university’s High-Speed Wind Tunnel facility was finally ready for its first experiments.
“You have no idea how I felt when this equipment arrived,” says Rocha, a professor in the Department of Mechanical and Aerospace Engineering whose research on aeroacoustics, structural acoustics and turbulence modelling is aimed at developing quieter aircraft.
“It’s a big milestone,” continues Rocha, who designed the chamber and components with her team, providing manufacturers Eckel Industries and HTS Ottawa with the drawings they needed for construction. “It means that the basic foundation for my research is now here, and that my students and I have access to a state-of-the-art setup that’s unique in Canada.”
The test section — a chamber with thick walls and a thick door — looks a like a recording studio. The interior is covered by acoustic insulation wedges sheathed in perforated metal to deaden sound.
Four large floor-to-ceiling air tanks with a total volume of 26 cubic metres, powered by a 100-horsepower compressor, are connected to the chamber through a custom designed nozzle which can send air into the test section at speeds of up to Mach 1.4 — 40 per cent faster than the speed of sound.
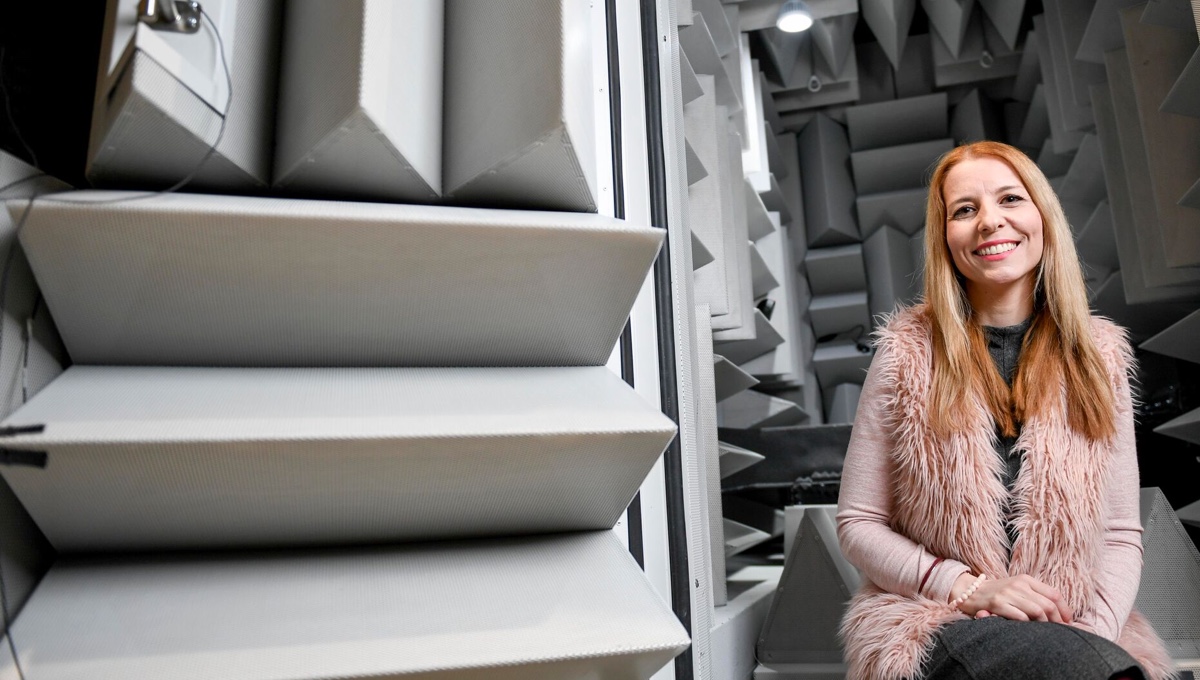
Although preliminary experiments remain within the Mach 0.3 to 0.8 range and are focused on using extremely sensitive microphones to record the sounds of air flow to gain a better understand of turbulence-induced noise during flight, the test area is adaptable in myriad ways and can also be used to assess the performance of wings, fuselage panels and other aircraft components.
“We don’t want to close any doors,” says Rocha. “We plan to add new features and modify the chamber if required over time to pursue multiple research directions.”
Typically, explains Rocha, computer models used to predict turbulence-induced noise must be validated with expensive flight tests. “With this equipment,” she says, “we’re aiming to develop wind tunnel testing frameworks which closely reproduce Mach conditions during flight, possibly decreasing the number of flight tests required, to improve existing acoustic prediction modelsand help develop novel and quieter aircraft structures. This is a natural evolution for my research.”
Less Noise is Safer
Reducing noise inside and outside airplanes in flight is a safety issue as well as an element of comfort for passengers and crews in a competitive global industry where traffic is expected to double within two decades.
Aircraft noise — which can come from the engine and turbulent air flow around the fuselage, wings and landing gear — is an economic issue, too. Airports that face flight restrictions due to excessive take-off, flyby and landing noise can’t optimize their operations.
Rocha, who has expertise in both air flow and sound, differs from most engineers who traditionally focus on just one of these areas. She also connects noise to environmental sustainability. An “elegant” airplane with an aerodynamic engine and structure will be both quieter and more fuel efficient.
One of her current projects is funded by the Consortium for Research and Innovation in Aerospace in Québec (CRIAQ), and involves collaboration with Bombardier Aerospace and MDS Corporation, and with colleagues at the University of Toronto and the Universitéde Sherbrooke, with additional support from the Natural Sciences and Engineering Research Council of Canada.
Two of Rocha’s graduate students are conducting tests with the new equipment in Carleton’s Mackenzie Buildingand Minto Centre, with students from U of T and Sherbrooke and possibly professional engineers from Bombardier and other aerospace companies, as well as the National Research Council and the German Aerospace Center (DLR), coming to use it too.
Everybody must leave the High-Speed Wind Tunnel lab when experiments are underway because the sound and air pressure are so intense. They can watch from the control room, and results are logged by a computer for data processing and analysis using customized software.
“There’s a lot of potential for our team to develop new models that can predict turbulence-induced noise during flight,” says Rocha, explaining that previously she and her students and collaborators had to do tests using a low-speed wind tunnel and extrapolate the results to replicate flight conditions, which is not as accurate. “Ultimately, this will help us develop better aircraft structures, such as more efficient wing shapes, fuselage panels and landing gear.
“It’s extremely rare,” she adds, “for students to be able to use this kind of setup. They’ll be doing design work, testing ideas, taking measurements and processing signals — all very valuable skills, which will not only be helpful for Canada’s aerospace industry but also their future careers.”
Friday, March 16, 2018 in Aerospace, Engineering
Share: Twitter, Facebook